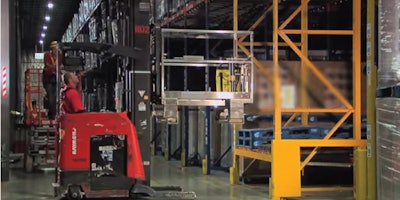
CASE STUDY: PROCTOR & GAMBLE
THE CHALLENGE
Proctor & Gamble distribution centers, such as Brantford, Canada, have grown to become large centralized
facilities typically exceeding one million square feet of fast moving consumer goods. To obtain maximum
efficiency and ROI, high density storage solutions are utilized. In this case push back racking up to 6 pallets
deep. This can present significant challenges. Push back rack is prone to jams caused by issues such as
‘chunks’ of pallet caught in the guide wheels, and spilled loads of product. These challenges lead to out
of service pallet positions. For many years these problems were corrected by ‘man handling’ at height.
However, racking structures are not engineered, nor approved anchor points. For this reason, Proctor &
Gamble made the firm decision to stop all climbing inside high-density rack structures at height. The result
of this action was lots of yellow caution tape, and a scramble to find a solution. Clearly, the repercussions
of accidents, injuries, and worse, cannot be tolerated as a caring and fiscally responsible company.
THE SOLUTION
Proctor & Gamble had, in fact, been searching for many years for a commercially available solution.
However, the solution involves more than a hardware product. It requires a complete process from start to
finish, backed up by R&D, testing, and validation by safety experts and accredited professional engineers.
The approved solution was IRONguard™ Safety’s MARC™ (Maintenance and Retrieval Cart). The MARC™
is a self-propelled engineered anchor system that provides operators with a ‘safe zone’ at any location at
height and depth in the rack system. It is loaded using common material handling equipment. Operators’
transition to the MARC™ via an approved man lift. Special tools and procedures were developed in tandem
to the hardware enabling a variety of tasks to be accomplished safely. Not only can operational deficiencies
be remedied quickly, but also maintenance, inspection, and repair (in otherwise inaccessible areas) can be
accomplished with minimal risk.
THE RESULTS
The challenges that created risk, frustration, and an undefined approach to remedying all the culprits,
turned into a safe, strategic, efficient, and documented process from start to finish. Even the dynamics of a
variety of spill scenarios are first analyzed by the newly created ‘spill assessment team’. Internally created
SOP’s accompany this new approach. In addition to reduced risk, this innovation creates a predictable
system to avoid these operational risks. There is now also minimal product spoilage (due to expiry dates
overrun by stuck product at height) and damage of product falling to floor level.
At Proctor & Gamble, IRONguard™’s MARC™ signified a passion to solve the problem by caring and
thoughtful ‘team members’.
TM
TM
TM