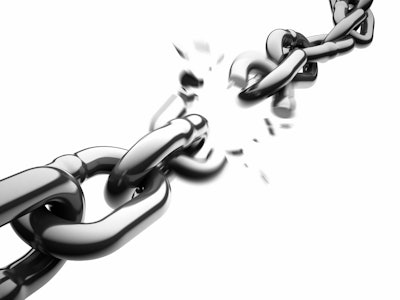
Industrial Distribution had a chance to speak with Siva Paramasivam, the Senior Manager of Supply Chain Operations at Deloitte Consulting, a company that helps Supply chain organizations continue to grapple with globalized markets and operations, pricing pressures and increased customer expectations. In this challenging environment, forward-looking insights combined with disciplined execution can help organizations ensure that their supply chain is healthy and robust, helping to assuage the impact of unexpected chaos, like the recent Hurricane Sandy that hit the east coast.
What can a company do to prepare themselves, their employees, and their supply chain for an interruption as large as Sandy?
Unexpected disruptions like Sandy serve as reminders that it is nearly impossible to predict and prepare for every type of risk. Instead, companies are better off focusing on the vulnerabilities that expose them to these risks in the first place and building resilience in their supply chains. Resilience can be enhanced by focusing on core supply chain capabilities around visibility, flexibility, collaboration and control.
What sort of emergency plans and procedures should a company have in place prior to an interruption like this?
Business continuity plans are critical. They have become fundamental for businesses nowadays. They are almost “table stakes” for operating in the current macro-environment. However mature supply chains should go beyond the procedures to proactively built resilience to overcome disruptions in the critical nodes – be it a key supplier or a distribution location.
Once a disaster does strike, what is the number one thing in terms of the supply chain that needs to be made a priority?
People. Contingency plans and responses should ensure that the safety and wellbeing of employees and other stakeholders are taken care of first. Communication across the extended value chain is critical to ensuring these stakeholders are taken care of as well.
How do you notify your customers of the impact? How much information is too much information – or too little? How soon after the incident? How long is too long to wait?
Customer communication is critical. At one end of the spectrum, companies in certain industries, like engineered products, hi-tech etc. need to collaborate with their customer partners both proactively to be prepared for possible impacts and also reactively to overcome any disruptions. In these cases, the visibility across the value chain and level of communications needs to be very high. But in most cases, the minimum expectation would be to keep the customers updated on the impact and response – from the onset of disruption to complete recovery. Such a strategy obviates potential for confusion and in fact can drive collaboration.
How should employees be trained to handle situations like this?
Simulation and table-top exercises are an extremely effective way to prepare employees and stakeholders. Even with extensive plans in place, exercises like war gaming can play a key role in helping companies understand the potential impact. In particular, they demonstrate the impact on stakeholders upstream and downstream while testing the robustness of the mitigation plans.
For more information about Deloitte, visit www.deloitte.com.