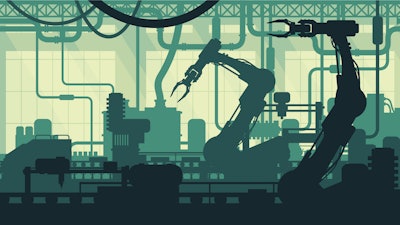
Could COVID-19 be the catalyst for a "lights-out" factory? While 67 percent of manufacturing decision makers say their adoption of digital technologies has accelerated as a result of the pandemic, one expert in particular believes this doesn’t mean fully automated factories are in our near future.
Manufacturing.net recently spoke with Ken Koenemann, vice president of technology at Dploy, who says a lights-out factory is not an immediate reality. Why? Until machines can fix themselves, there will still be a continued need for human talent.
Manufacturing.net: As COVID-19 has advanced manufacturer’s use of digital technology, what is the key to getting automation right?
Koenemann
Manufacturing.net: What should manufacturers consider while assessing whether automation is right for them?
Koenemann: It’s all about what is adding value for your business. When you look at processes, only about 5% of what is being done is truly value-added (which means material is being transformed into a product or data that the customer is willing to pay for). So, when assessing whether automation is right for you, think about where the non-value added activities are in the process and what can be done to automate those processes. What is the value that it is going to bring? Could it improve quality and reduce scrap? Could it improve productivity?
Again, there will always be a human component here. Manufacturers need to evaluate whether they have the right human skill set that can take care of problems with technology if they arise. Because let’s face it – they will.
iStock
Manufacturing.net: What are the downfalls of a lights-out factory?
Koenemann: What many people forget about a lights-out factory is that in the world of manufacturing, there has and always will be, problems that arise constantly. While the concept is great, until technology is able to address issues themselves – we will need humans in the factory to do so. Think about it: the only people doing lights-out factory automation are those that need a machine to run for an extended period of time. Until assembly lines have nanotechnology and can fix themselves, machines will go down.
Also, think about the culture of this. You’ll still need talent in the factory – and who wants to work in such an isolated environment? We all know finding the right manufacturing talent is already tough and top recruits are going to pass on these opportunities because they want the human aspect in order to be trained to progress their skill set and career.
Manufacturing.net: What do you forecast is to come during the next 10 years for manufacturing technology and machine learning?
Koenemann: In the next 10 years, we’re going to continue to see the evolution in technology that can be used in manufacturing. Think about this: cell phones have only been around since the late 1980’s and there’s been so much evolution. Plus, the pace of change is going to continue to accelerate and we’ll learn more and more about how to use technology in manufacturing. Also, more manufacturers are making technology decisions because of the COVID-19 pandemic. They’re thinking: how can we automate some of this stuff and not be so reliant on people? Massive amounts of the workforce couldn’t go into the factory, and/or deciding not to return, creating a huge problem.
Consider machine learning. We need to remember that in order for this to be successful you have to teach it to recognize patterns – meaning you have to give it a ton of data. Keeping in mind you also need staff that are experts in this field, and there’s a massive cost with employing data scientists.
Essentially, while automation sounds like it’s going to win every time, it won’t. It’s important to not get carried away with technology’s hype and forget about what is practical. Technologies will evolve over the past 10 years and new technologies will be introduced. While technology will be beneficial for manufacturers they still need to proceed with caution when determining the right automation, machine learning or any digital technology that brings value to the business. If manufacturers implement manufacturing technologies for technology sake that is a big mistake. There are downfalls to some technologies, and while certain things might work for technology companies, they may not be the right fit for manufacturers.
Manufacturing.net: What role does reskilling the workforce play as automation continues to progress in manufacturing?
Koenemann: As you bring more technology into your business, you must have the right people that can manage and use that technology. Which means, over time as you add more technology with different capabilities, you will also need to modify your employee roster appropriately, by adding people with different skillsets that match the new technology.