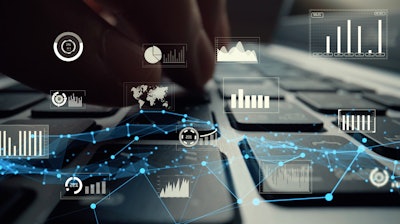
It’s no secret that manufacturers and distributors are relying more heavily on automation than ever before. In fact, the automated storage/retrieval system (AS/RS) market is expected to reach $27.68 billion by 2027. In order to stay ahead of evolving technology, warehousing professionals are realizing the importance of software applications, specifically Warehouse Management Systems (WMS) and Warehouse Control Systems (WCS) to help distributors move products faster, help create optimal inventory levels, and improve order fulfillment accuracy.
In warehousing, it is not uncommon to have a WMS and WCS operating as separate applications with the WMS managing the workflow of the operation, while the WCS executes the workflow within automation. Yet without a seamless integration, the combination of these applications can lead to unnecessary challenges. Supporting these systems individually often requires valuable time, resources, and capital.
Implementing a Warehouse Execution System
Automation is only as effective as the software that controls it, and any intelligent warehouse would greatly benefit from a properly managed Warehouse Execution System (WES). A WES saves time and ensures effective, inter-process communication by providing a plethora of actionable insights through appropriate data analytics. A WES offers an integrated set of WMS and WCS functionality within one application, simplifying warehouse communication and reducing the need to manage several applications. Additionally, a WES platform can bridge an enterprise resource planning (ERP) application with the WMS applications, optimizing order flow, overseeing process flow, and directing material handling equipment and warehouse automation.
This solution is ideal for organizations with increased order volumes and high throughputs. It is able to receive and track products while tying inventory to specific customer orders through its order fulfillment processing capabilities. As orders come in, the WES breaks them into logical units of work and then utilizing its WCS functionality, directs automation or manual labor to execute the job. The WES provides the overall coordination of WMS and WCS functionality, such as inventory and order management, billing, and workflows, within a single application.
The Benefits of an Integrated WES
Operating as a two-in-one solution, a WES has many clear advantages over traditional, individually implemented WMS and WCS systems, like:
- Simplicity: A WES requires a reduced need for complex integrations due to the built-in WMS and WCS features.
- Time-Savings: Less time and fewer resources are needed to ensure effective communication between the WMS and WCS.
- Flexibility: A WES offers the flexibility needed to interface with additional applications and host systems, such as ERPs, PLCs and other automated equipment.
- Consistency: Having a single application across an organization helps ensure processes are consistent and efficient.
- Cost Savings: With a WES functioning as a single application working alongside automation, organizations can increase inventory accuracy and reduce labor costs.
Additionally, an integrated WES provides product traceability allowing manufacturers and distributors to efficiently handle recalls and comply with regulations. A WES can help discover and act upon issues contributing to a recall more efficiently, helping manufacturers to identify what product is recalled and reducing the number of products that are released to the public.
Utilizing a WES that is integrated with WCS and WMS capabilities, as well as other supply chain systems, helps warehouse personnel to work more efficiently, increase inventory accuracy, and improve product traceability.
Steps for Increased Capability & Functionality
Although a WES that also includes WMS and WCS functionality could replace existing WMS and WCS applications, it is also flexible enough to adapt to a variety of deployment options. Warehouses with an existing WMS will look to introduce a stand-alone WCS to assist with automation; however, it might be best to bring in a WES with integrated WCS functionality instead. Doing this allows the company to continue using its original WMS and integrate it with the WES to leverage its WCS and integrated process capabilities. Alternatively, if the organization has not introduced automation and therefore does not need WCS functionality at first, it can still implement the WES with integrated WMS capabilities and activate the WCS functionality when appropriate with future automation. Integrating the WMS and WCS together within the same application often results in reduced training times and shortened start-up time when new functionality is desired.
Finding the right partner to help you analyze your needs and implement a WES tailored to those needs is crucial. With a sophisticated WES, you can orchestrate the process across your facility, resulting in a warehouse that delivers better product traceability, storage usage, increased inventory accuracy, and allows for growth and flexibility to accommodate ever-changing warehousing needs. As the need for automation continues to grow, so will the need for an integrated warehouse execution system.
Dave Williams is the vice president of technology solutions at Westfalia Technologies.