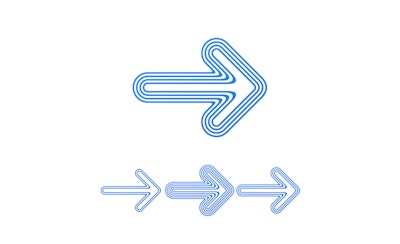
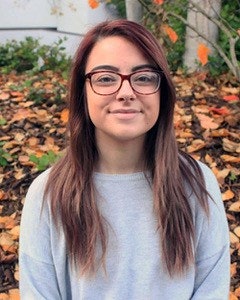
In the competitive world of business, you may be facing the disadvantage by keeping too much inventory. It’s estimated that anywhere between 20 and 30 percent of a company’s inventory is dead or obsolete. This will not only tie up cash, limit storage space, and drive up handling cost, but excess inventory can cause safety issues and problems in quality. Lean manufacturing seeks to improve production by eliminate these wastes, delivering high-quality products while operating as efficiently as possible. Having a practical system to control and schedule inventory led Toyota engineer Taiichi Ohno to develop Kanban.
Kanban, a Japanese term that roughly translates to signboard or billboard, is a scheduling system to improve efficiency and flexibility in manufacturing. In order to implement an effective Kanban system, it is important to understand the tools and core principles of Kanban, as well as Toyota’s six rules for success.
After some development by Ohno, Kanban was integrated into the main plant machine shop of Toyota in the 1950s. A physical card was passed downstream through the production line to signal the next step. Materials were able to move smoothly through the facility and, consequently, excess amounts of inventory were successfully avoided. The success of this system meant Kanban quickly caught on. Kanban has now been adopted by companies worldwide and is a staple for Lean manufacturing.
Toyota revolutionized production when they introduced just-in-time (JIT) manufacturing, a process that operates on a pull system rather than the traditional push system. Historically, production was scheduled by forecasting customer demand and supplies. Materials would then be purchased based on this prediction. Products were processed to meet the forecasted demand, which can often be inaccurate. Companies could be left with large amounts of inventory and dealing with particularly long lead times.
On the other hand, a pull production system is controlled by customer orders as they come in. JIT aims to balance inventory levels with actual demand by leveling the rate of production to match the rate of consumption. This approach avoids or eliminates the wastes of excess inventory, overproduction, and over-processing. JIT production is a manufacturing model and Kanban is the ideal tool to achieve it.
Kanban is an inventory management system that supports the entire production system while encouraging continuous improvement in the workplace. It utilizes the use of cards, bins, and other visual signals to facilitate communication not only within the production process, but also with suppliers, consumers, and buyers. In a manufacturing facility, visual cues are systematically sent to a department, team, or supplier that will trigger an action to ensure replenishment.
When designing your Kanban system, you will want to choose the Kanban tools that are going to work best for your business and tailor the system for your specific workplace.
- Kanban Cards: Cards are typically used for managing larger items in inventory and are passed down the line to either signal an alert for replenishment of supplies or to trigger production. Kanban cards include all of the important and specific information for each stage of production and what supplies or materials are needed at subsequent processes.
- Kanban Bins: Bins are often used for managing smaller inventory items, like nuts and bolts, within the manufacturing process. For example, one step of production has a two-in system. Workers pull the materials from the first bin as needed until it is empty, moving on to pulling from the second bin while the empty bin is sent to be replenished. By the time the second bin is empty, a full bin has already been placed back into the work cell, and the cycle continues.
- Kanban Boards: A simple Kanban board is typically divided into three columns: “Requested” or “To Do,” “In Process,” and “Done.” Orders are written on cards and are moved from column to column. This allows people to see the work in process easily and track orders as they move through the process.
- Electronic Kanban: Kanban has evolved with technology and allows facilities to transition from physical cards, bins, and boards to an electronic system that utilizes a barcoding system.
Depending on the size and complexity of the processes in your facility, you may have a Kanban with many moving parts and a combination of tools. It can get complicated, but Toyota developed six rules for ensuring an effective Kanban system:
- Defective items and incorrect amounts are not moved on to the next process.
- Items moving through the production process must be in a bin, accompanied with a card, or tracked in the electronic Kanban system.
- As processes use supplies, Kanban requests are issued and sent to its suppliers.
- Each process produces the exact quantity and in the order of incoming requests.
- Nothing is produced or moved without a request.
- Kanban requests are limited to reduce inventory and uncover inefficiencies.
Additionally, adhering to the four core principles of Kanban methodology will help your workplace, managers, and employees understand the best practices for a successful system.
- Visualize Work: Use a value stream map to create a visual model of your workflow. Using a whiteboard or poster board, map out the flow of materials as it moves from process to process. This will allow you to clearly see how the manufacturing process is operating and identify areas of improvement.
- Limit WIP: WIP falls under the umbrella of inventory and having an excess of unfinished products will cost your business time, money, and space. WIP limits are a fixed constraint set internally that can be placed on teams, departments, or individuals. For example, setting a WIP limit of seven products, this means only seven items can be in the production system at any given time. Establishing an upper-limit for WIP includes a little bit of experimenting and some trial and error, but it is a tool that will help you reach the full potential of Kanban.
- Focus on the Flow: In order for Kanban to be effective, you must create a solid foundation by streamlining and optimizing workflow. Look at the VSM you created and look for bottlenecks in the production process and identify areas with frequent unplanned stoppages and where materials sit for an extended period of time. With your team, decide on a handful of small changes, add them to the map, and begin implementing them slowly.
- Continuous Improvement: Kanban isn’t a system you implement, and it’s considered finished. Like other lean manufacturing tools, it is important to evaluate the system with continuous improvement in mind. Check in daily or weekly to see how the system is working and gather input from employees. Make changes as you see fit and remember, there is always room for improvement.
Having enough inventory to meet demand is important, but too much inventory will cost your business. Sustaining a sufficient amount of inventory will keep processes running smoothly and bring problems to the surface, allowing you to fix them quickly. Kanban is a practical solution that allows you to address the wastes of excess inventory successfully schedule and control inventory, dramatically improving your manufacturing efficiency.