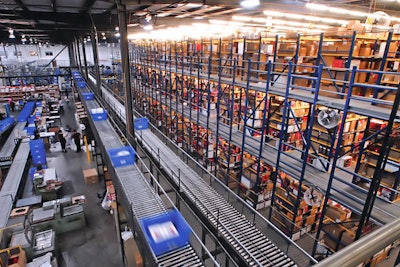
After experiencing a period of significant growth, you realize that your remaining warehouse space is limited. Your facility is maxed out, and you’re receiving pressure from upper management to meet these growth needs. In order to accommodate your booming business, you immediately decide to embark on an expansion project and begin weighing your options. Should you build a brand new warehouse, utilize an off-site storage facility, or expand the current facility?
Although these options will certainly generate more space, in actuality, the general construction will yield nothing to ROI and add minimal value to the growth process. Instead of opting for expensive new construction, you may be overlooking the most practical solution, your existing facility. All you need is the right type of automation.
By retrofitting your warehouse with the right automation technology, you can easily leverage your existing assets and real estate to accommodate growth. Retrofitting opens the door for many new opportunities and benefits that new construction would not provide. Introducing high-density automated storage/retrieval systems (AS/RS) can increase the warehouse’s storage capacity without expanding the facility itself. Oftentimes, AS/RS can increase the storage space dramatically so that you can effectively manage your growth on site. It is also possible to integrate other capabilities into the AS/RS with the existing warehouse, including order fulfillment case picking to go along with unit load demand. As a result, you get even more value out of your investment.
Second, it is easier to justify the cost of automation systems if the general construction can be reduced or eliminated from the equation. Facilities themselves do not generate ROI and only dilute the return for the automation being considered. To reiterate, with automation, you’ll not only eliminate the element of new construction, but also receive the added benefits of increased productivity, greater inventory accuracy, and improved ergonomics. Although you’ll contribute capital to automation upfront, the pay-off will be well worth it — typical AS/RS ROI is three to five years, and the systems have lifespans of more than 25 years.
From a “green” perspective, automating an existing facility is the clear winner over new construction. Obviously, automating the existing facility, rather than increasing land usage by building new structures, reduces your organization’s carbon footprint. Within an automated facility, you’ll realize even more eco-friendly benefits. Besides reducing labor with the automation, AS/RS can run in a “lights out” environment, leading to energy savings. Similarly, eliminating the need for gas or electric-powered fork trucks reduces emissions from engines or battery charging areas.
Today, automation delivers such a high-level of performance and reliability that it is in your best interest to investigate the technology. If at all feasible, utilize existing real estate assets and automate what you have. You’ll eliminate new construction while, at the same time, automate your processes to position your warehouse for greater efficiencies and future growth.
Gary Frank is VP of automated systems at Westfalia Technologies, Inc.