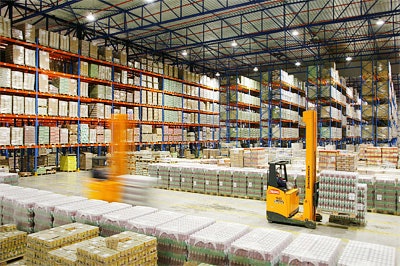
Complete this phrase: "Lean _____."
If you answered “manufacturing,” you’re probably in the majority. However if you didn’t at least consider the possibility of using “warehousing” too, your company may be missing out on substantial supply chain savings.
That’s what my organization discovered eight years ago when we started using Lean at many of our distribution centers. Nearly 1,000 projects and $47 million in documented savings later, we have every reason to believe this highly popular quality improvement tool is as applicable to logistics as it is to production – and numerous real-life suggestions for how your company’s warehousing facilities can apply it just as successfully.
Streamlined Pallet Performance
Pallets and distribution centers may go hand-in-hand. However that doesn’t mean that every pallet in a warehouse is essential – or pulling its full weight – which is why projects that address these ubiquitous pieces of equipment often deliver the kinds of quick wins that Lean teams and their organizations love.
By doing a project that resulted in a switch to slip sheets instead of wood pallets for most of its inventory, one of our facilities’ Lean teams pared thousands of dollars from operational expenses, all while speeding up product handling and reducing product damage. Meanwhile, after executing a three-week project that focused on increasing the average number of cases shipped per pallet through better pallet optimization, another managed to shave $500,000 off its location’s total costs.
Even something as simple as how and when pallets are inspected can make a big impact, as one of our Lean teams learned when its project findings included a recommendation to inspect pallets during receiving instead of later. This slight modification enabled the facility to eliminate the wasted time its workforce had to spend changing out any wood-damaged pallets they came across during order picking – and save $60,000.
Better Performing Configurations
It goes without saying that the positioning of your company’s key warehousing elements like pick lines, and conveyors has probably already been carefully mapped out by highly trained engineers and/or optimization tools. Even so, don’t be surprised if your Lean teams discover that there’s still plenty of room for improvement in this area.
One of the most successful teams in our Lean program’s history helped its facility derive $1.1 million in savings thanks to a two-week project that led to a change in the layout of the facility’s work stations and conveyors.
Another succeeded in making its order pickers more productive by multiple pieces per hour via a project that focused on re-organizing pick lines by weight and product type, with the heaviest products first; this created thousands of dollars in annual savings.
Some operations have even yielded good financial results simply by changing the location of their label printers.
Less Overflow And Overtime
And then there is the issue of seasonal shifts or sudden surges in demand. Lean projects that address how your company can weather these peaks without having to resort to extra facilities or extra-long work days could open the door to facilities that work considerably smarter rather than harder – and healthier balance sheets your finance department will applaud.
For example, one of our Lean teams examined how space in several existing warehouses could be better utilized so that a longtime warehousing client could reduce its heavy reliance on overflow facilities. The result was an improved replenishment process for pick areas, more double-stacking on storage racks’ highest levels, greater use of space in previously empty areas like the square footage around dock doors, and $1 million in annual overflow warehousing savings.
Another tackled the challenge of a long-running facility’s order flow and work requirements so that its client could reverse the trend of escalating overtime expenses, a project that culminated in a change of work shifts. This ultimately allowed the work load to be more evenly distributed and reduced overtime-related labor costs by $200,000.
Tackling Transportation Inefficiencies
By now, it should be apparent that there’s almost no limit to the kinds of things your warehouses’ Lean teams can tackle and improve – and no boundaries. In fact, some of your company’s biggest wins may come from projects that address what’s happening outside of, rather than, within your facilities’ walls.
Such was the case when a Lean team at one of our facilities engaged in a project that involved gathering more accurate dimensional data on outgoing truckloads and then using that upgraded data to create better truckload optimizations. This enabled the facility’s client to increase each of its loads by 200 cases per truck, reduce its shipping needs by 120 trailer loads per year and save $350,000 annually.
And that was just a drop in the bucket compared to the potential savings uncovered to what one of our South America-based teams decided to focus on helping its client minimize the sky-high container demurrage charges it was having to pay when so many of the trucks carrying its inbound inventory wound up routinely getting stuck in the Andes Mountains due to bad winter weather. Its simple recommendation – moving more inbound shipments traveling to Chile from Argentina and Brazil by water instead of truck – wound up shaving $1.8 million off its client’s annual demurrage bill.
The Final Word
These projects are by no means representative of all the possible ways your company can apply Lean to its supply chain. In fact, as any experienced Lean practitioner can tell you, they’re merely the tip of the iceberg.
However they all share several common traits: Each was executed by supply chain professionals who probably have the same kinds of skill sets as the people employed at your supply chain operations. Each was completed without pulling any one employee away from his or her day-to-day responsibilities for too long. And in the long run, each helped changed its operation and overall corporate culture for the better. Most important of all, each represents the kinds of positive changes and results that are just as attainable for your distribution centers, provided your organization is willing to take the plunge and give Lean warehousing a try.
So go ahead. Test it out at a facility or two. Research other Lean best practices on the web. Or feel free to reach out to other Lean professionals to get their input. What have you got to lose – except a lot of waste and inefficiency?