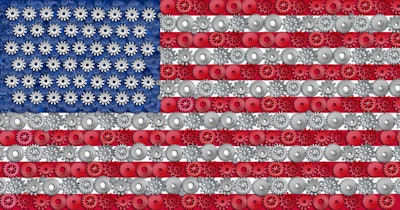
In a far-ranging recent interview on CBS’s “60 Minutes,” Apple CEO Tim Cook talked about a variety of issues affecting his company, but his comments as to why the tech giant outsources its manufacturing raised a few eyebrows in the industrial marketplace.
“It’s skill,” Apple CEO Tim Cook said in response to a question on Sunday from CBS correspondent Charlie Rose as to why many of the company’s products are made in China.
Rose, looking surprised, asked: “They have more skills than American workers? They have more skills than German workers?”
Cook’s response came quickly.
“The U.S., over time, began to stop having as many vocational kind of skills,” Cook said. “I mean, you can take every tool and die maker in the United States and probably put them in a room that we’re currently sitting in. In China, you would have to have multiple football fields.”
Does Cook have a point?
According to the Bureau of Labor and Statistics, the number of tool and die workers has dropped 24 percent in 10 years while the mean hourly and annual wages rose 14 percent. In 2014, there were 477,000 people employed as tool and die makers and the outlook is for a six percent increase from 2014 to 2024, about average for overall employment. Workers familiar with computer software applications and who can perform multiple tasks in a machine shop will have the best job opportunities in the future, BLS said.
Machinists train in apprenticeship programs, vocational schools, community and technical colleges, or on the job. Tool and die makers receive several years of technical instruction and on-the-job training.
But the 6 percent growth for tool and die makers is not acceptable, especially if manufacturing is to continue growing in the years ahead. It is the same for many other skilled jobs in manufacturing and with many factory workers retiring, the problem is only exacerbated.
Vocational education, as Cook noted, is not stressed by guidance counselors at high schools nor is manufacturing even advocated by parents as a career opportunity. Specifically, 37 percent of parents would not be in favor of manufacturing as a choice for their children while more than half (52) percent of teenagers said they have no interest in pursuing jobs in manufacturing, according to a study by the Manufacturing Institute last year.
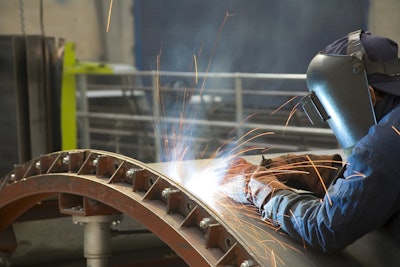
Here is what Forbes magazine had to say about vocational education: “The demise of vocational education at the high school level has bred a skills shortage in manufacturing today, and with it a wealth of career opportunities for both under-employed college grads and high school students looking for direct pathways to interesting, lucrative careers. Many of the jobs in manufacturing are attainable through apprenticeships, on-the-job training, and vocational programs offered at community colleges. They don’t require expensive, four-year degrees for which many students are not suited.”
A few years ago, Industrial Distribution conducted a study showing that the average age of an employee on the plant floor was 56 years old. That average age has increased, and with many of them retiring, there are fewer young people who want to take on those jobs.
Other manufacturers and distributors are facing the same problem.
Last year, I spoke to a group of welding executives who told me their number one problem was finding qualified employees. These business owners had well paying jobs available but there weren’t enough workers despite the pay, which started at more than $50,000.
With overtime, the pay can be lucrative. In fact, one newspaper article focused on a graduate of a welding program, a 24-year-old male who made more than $100,000 after three years in the business when overtime was factored in.
A power tool manufacturer also told me he could run three shifts but was only using two because he couldn’t find the people with the right skills or who were willing to be trained in manufacturing.
The Manufacturing Institute’s study titled “The 2015 Skills Gap” identified the top 5 reasons identified as to the impact of lack of skilled talent and the reasons for it. Here are some of the highlight.
1. Over the next decade, the skills gap is expected to result in 2 million manufacturing jobs going unfilled, in part due to baby boomer retirements and economic expansion.
2. It takes more than 90 days to recruit highly skilled workers like engineers, researchers, and scientists.
3. 70 percent of executives indicate current employees are not sufficient in technology/computer skills.
4. Only three out of 10 parents would encourage their kids into manufacturing as a career.
5. Gen Y (ages 19-33 years) respondents ranked manufacturing last as a career choice.
So, why do we need an increase in U.S. manufacturing? Every job in manufacturing creates another 2.5 new jobs, according to the National Manufacturers Association. Manufacturing is a critical component to the overall success of the United States economy.
Apple, for example, has more than 40,000 employees working in the United States and about 20,000 overseas. Much of the manufacturing work is contracted in companies in China, Europe and other countries with hundreds of thousands working on Apple products.
Could that change in the future?
The New York Times reported that the late former head of Apple, Steve Jobs, once suggested at a conference it might be possible someday to locate some of Apple’s skilled manufacturing in the United States if the government helped train more American engineers.
In the meantime, however, Apple and other large companies will continue to conduct a large portion of manufacturing overseas. That’s not good news for the U.S. economy.