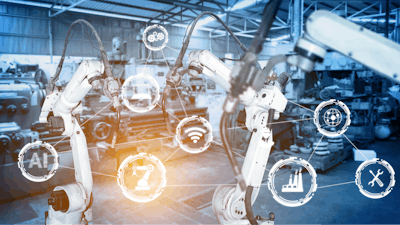
Humanizing organizations are those that prioritize workforce effectiveness over machine efficiency.
Admittedly, humanizing organizations are currently a small subset of the companies involved in industrial production. No one organization is 100% humanizing all the time, because it is a complex journey with stops and starts.
Over the past decade, we have observed humanizing practices at play at German industrial tool maker DMG MORI, U.S. manufacturing company Stanley Black & Decker, and at life science giant J&J, as well as in a plethora of other companies big and small. These observations have been made while implementing technology. This might sound strange, but it is not. Industrial technology requires engineering prowess, for sure, but as we describe in our book Augmented Lean, implementing it to good effect remains an intractably human challenge.
Making technology work means prioritizing technical interfaces that allow its users to have strong input and that don’t alter too many of the ingrained processes already in place. The metaphor from woodworking would be just that, working with the grain so the wood doesn’t splinter. A splintered workforce is neither effective nor efficient. Smoothing surfaces against the grain is highly risky.
Augmented Lean is a management framework where workers count as much as leaders, if not more. That follows from the observation that each human employee has a near endless value from being primarily persons, only secondarily performing in the role as workers. If there are more workers, they could in some ways be more important as a group than those who lead them, although, we admit, such calculations are somewhat meaningless. We prefer to think of the workforce as a system where all parts of the organization need to be augmented in order to achieve sustainable productivity.
Either way, with such a perspective the operations function in an organization changes characteristics. Operations becomes a challenge of optimizing a collective, using leadership as “sandpaper” with no intrinsic value except as input in shaping a material end. Operations is certainly not about perfecting a group of leaders who are free to use whatever resources they command or corral.
Eight principles should rule the era of augmentation. Implementing them requires lifting the perspective to try your hand at Humanizing Organization Operations Principles (HOOPs). They are truly hoops, meaning challenges leaders need to overcome in the pursuit of a better, more efficient organization that works for people, not just for machines. Augmented lean organizations demand something fundamental from their humans, leaders and workers alike: their full attention. And the challenge amounts to a feat similar to simultaneously woodworking and attempting to hit basketball hoops-it requires ambidexterity.
The eight principles that should rule the era of augmentation are: learn, empower, augment, decentralize, enable, respect, hack, and govern (LEADER/HG):
- Learn: Every process starts and ends with learning, reflection, and applying what you learn to the next challenge.
- Emerge: All initiatives should emerge bottom-up, be human-centric, should rely on self-service, and must be implemented in low-code/no-code apps to avoid excluding wide parts of the workforce.
- Augment: Build human capability, don’t just replace or automate.
- Decentralize: Localize responsibility and control, consider operations as a network of people, sites and systems.
- Empower: Think hard about how to empower each part of the system affected by your activities: workers, managers, plants, factories, locations, and communities.
- Respect: Respect all levels of the system, e.g. the process, the system itself, the ecosystem, the individual, the workers, and as a worker, you need to respect managers who try to move things forward with limited information.
- Hack. Ensure all tasks, and the overall system remains open, agile, adaptable, Lean, and, importantly, follow Kaizen ideals (“always improving”.)
- Govern: Once an initiative is underway, you should attempt to standardize, clarify, and create a platform for innovation, but don’t overdo it so employees lose the initiative to improve, iterate, and innovate.
Because these eight principles are multifaceted challenges, they don’t have to be accomplished in order. Great effects can be had by scoring five or more hoops, not all eight. Just like basketball, augmented lean is a team sport. The leader we allude to is no specific person but the sum total of workforce energy applied to the challenge. The top-down and bottom-up combination we describe does not have to be executed by different people either. In some cases, digital leaders have to improvise or hack as much as operators have to govern themselves because the ideal is near fully decentralized governance where most decisions are taken at the level the actions are expected to take place.
Beyond pure digitalization, HOOPs put priority on operations managers to enable sustainable change. Once that’s in play, HOOPs let workers themselves design their own process, production enhancement techniques, and tracking systems, which ensures less alienation, better user interfaces, and greater work satisfaction. Overall, HOOPs are about a new breed of emergent-governance, which is a combination of leadership and workers interacting with technology to change how a company works. To achieve that, we need to establish principles that value openness to change within certain constraints.
The leadership imperative becomes: “Leader: Hack and Govern!” – but not because they are process steps that need to be carried out in any particular order. Quite the contrary, we would be incredibly worried about using a waterfall technique to implement LEADER/HG. In fact, these are abstract principles that embody an overall approach. In fact, only implementing three or more of the principles, could potentially yield 80% of the benefits. Each principle is such a major culture shift that getting a handful of them right means setting the foundation for wholesale change.
Ultimately, any framework is simply an attempt to focus your attention on the most important aspects of your management practice, in a simplified manner that is memorable and shareable. Most conspicuous to many is our omission of Automate, the dictum of most industry 4.0 digitalization efforts. For us, automation is an interim process, but not a management focus or an end goal in itself. We should only automate to liberate humans to do more creative, value-added, and meaningful work.
Overall, there is truly only one principle that matters: humans first, automation second. This rule should apply even as the line between humans and machines will further blur as most of us slowly become augmented beings, with more and more essential tools and eventually body parts being augmented by technology in some fashion. Without such humanizing operating principles, we lose valuable organizational agency over automated processes which is a recipe for trouble in the future.
The augmented lean framework is not hard to understand intellectually, but it is tricky to execute because one group of persons does not control all the variables. This approach is counterintuitive to classic control theory and how IT leadership typically operates. However, humanizing organizations are not soft. They can be as fiercely competitive, ambitious, and demanding as any other organizational form. The notion of spending enough energy on the collective maintenance functions is what makes spectacular performance possible over time, it is what makes it sustainable.
Leaders who succeed at implementing augmented lean do like artisan woodworkers; start with the lowest grit, and sand their wood carefully, and keep switching to higher grit, even more carefully, the objective being to shape a structure towards meaningful uniformity but not to cancel out the inherent characteristics that made it distinct in the first place, all the while regularly shooting hoops which requires looking up.
Natan Linder is the co-founder and CEO of Tulip and co-founder and chairman of the board of Formlabs. Trond Arne Undheim is a futurist, venture partner, nonresident Fellow at the Atlantic Council, co-founder of Yegii, and lead ecosystem evangelist at Tulip. This article is abridged with permission from the publisher, Wiley, from Augmented Lean: A Human-Centric Framework for Managing Frontline Operations.