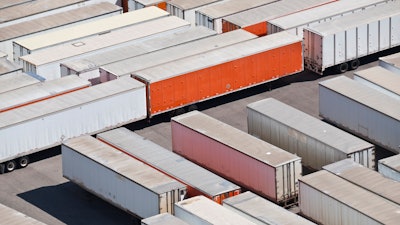
Properly managing the flow of trailers in and out of a yard is essential to manufacturers and distributors striving to run an efficient operation. Despite growing complexity, roughly 60% of all businesses still rely on manual practices for their yard management. This practice creates delayed receipt processing, delayed outbound shipments, higher detention costs and higher operational costs.
Sometimes, it makes operational sense to have outside drivers drop and hook trailers in the yard vs. live loading or unloading. Reasons for dropping a trailer vs. live unloading can include: trailers are unloaded by a crew on a different shift, the items on the trailer are not needed immediately, and more trailers arrive outside of set schedules than your operation can unload in a given day. Drayage outfits, total load carriers, and drivers prefer to drop and hook trailers as it is more efficient. Drivers can get in and out without waiting the standard two hours to be loaded or unloaded.
Let’s look at a typical scenario for a distribution company using manual processes to manage the yard. Trailers may or may not have a scheduled appointment. If there is a schedule, it is typically collected in Excel on Outlook. Trailers are checked in to the facility. This process is often delegated to security officers working the gate entrances. This is not ideal for the consistent application of a manual process because they are typically high-turnover lower-wage workers. Once checked in, the trailer is logged into a spreadsheet and the driver told where to park the trailer and which empty trailer to pick up, if one is available. When the items in the trailer are needed, the trailer is called up to a door for unloading, typically through radio communication. If the trailer is not located where the spreadsheet states it should be, the yard jockey must drive around the yard to find it. Sometimes, they cannot find it, prompting a change of plan to unload a different trailer, starting the process over again.
For manufacturers, inefficient yard management can cause just as many problems. Raw materials are often stored in trailers and consumed during production. Empty trailers are parked in the yard and used to store and transport finished goods to distributors and retailers. There are many drawbacks to manual processes. These can include: inability to plan an unloading crew’s shift properly, “losing” trailers in the yard, delays in unloading products, expensive detention charges for late trailers, inefficient use of yard locations, and time spent performing manual yard checks.
Most of the downfalls of a manual yard management process can be mitigated with a modern yard management system (YMS). When selecting a YMS, look for the following capabilities:
- Gate check in and out with radio frequency identification (RFID) capabilities
- Demurrage and detention tracking
- Rotational yard check to validate equipment locations
- Mobile move application for fleet, over-the-road, and yard jockey drivers
- A 3D view of yard locations and buildings with color status
- Built-in templates for inspections with image capture
- Reporting dashboards with analytics
- Workflow definition and automated task generation
- Scale integration and weight capture
A YMS will make managing your yard more efficient by providing real-time access to the following:
- Ability to track all trailers and railcars by equipment ID from the time they enter the yard until they leave at the enterprise and facility level
- Exact location of a piece of equipment at any time
- Contents of a trailer or railcar to identify hot shipments
- Current status of equipment (in or out of service), type of equipment, and who the owner is
As the adoption of artificial intelligence (AI) in distribution and manufacturing increases, companies can leverage these capabilities to determine the best placement of trailers for unloading. YMS software will be able to decide on the most efficient door for unloading based on a trailer’s contents and which bins or shelves they will be stored in. It can also help to meet safety and compliance goals using cameras and identifying anomalous events.
During a recent discussion with Christopher Grice, site leader at Grainger’s market distribution center in Denver, I asked if it is essential to properly manage trailers in a company’s yard. Grice said, “Trailers entering and leaving your facility should be treated as an asset. Maintaining visibility to those assets and what is on them should be seen as a critical part of the overall supply chain. With that in mind, there is a multi-faceted impact that can be derived from superior execution in this area, including improved customer experience through increased product availability, greater throughput and cost management tied to resource and staff planning, reduced risk associated with security and loss prevention, and ultimately helps to foster strong relationships with key external carrier partners.”
A YMS will also reduce the time it takes to process equipment at the gate, reduce your detention charges through visibility, and improve your service levels.
Will Quinn is the director of industry solution and strategy at Infor.