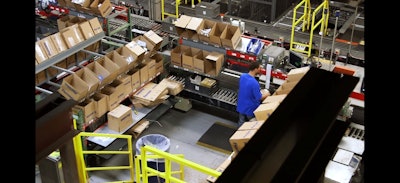
The 2018 State of Logistics Report, sponsored by 3PL Central, indicates warehousing models are evolving at a phenomenal rate. Online and mobile innovations are at the heart of increased traceability and visibility, and products must be delivered at break-neck speeds. More importantly, demand for warehouse space is at an all-time high, and warehousing is still short two million workers. Even with 5.2 percent of warehouses vacant, warehouse managers are still stuck with the challenge of maximizing warehouse space.
Poor Warehouse Utilization Increases Expenses
Poor warehouse utilization has been a key concern for supply-chain executives over the last decade. Labor regulations requirements (including safety and OSHA rules), picking practices, and order-fulfillment standards have evolved. Customer experience now takes priority over all needs in the warehouse, and in the age of e-commerce, the customer expects to order anything and everything. This has led to increased complexity in warehousing, increasing overhead expenses, and decreasing available space. As a result, warehouse managers need to turn to a new standard, using technology for maximizing warehouse space.
Using New Technology for Maximizing Warehouse Space Is the Solution
New technologies and warehouse automation are poised to enable warehouse managers to increase inventory without necessarily increasing space. The emergence of cloud-based platforms and Big Data increases forecast accuracy, eliminates unnecessary stock, and achieves truly optimized slotting designs. Since customers’ needs evolve on a continuing basis, warehouses must evolve in tandem.
Best Practices Are for Maximizing Warehouse Space
Embracing Big Data analytics and supporting omnichannel fulfillment options—including ship-to-store and storefront-as-a-distribution-center—can help warehouse managers fully utilize available space. Big Data can analyze picking performance and identify best practices to increase performance, effectively reducing the amount of on-hand inventory needed at any given time. Robotics can also be used to move large inventory, taking advantage of vertical space without sacrificing worker safety. As explained by the Lean Supply Chain, visibility and effective management of inventory are essential to maximizing warehouse space. Of course, it always helps to have a few tricks up the sleeve, so warehouse managers should follow these steps:
- Increase forecast accuracy using real-time asset and inventory monitoring and analytics.
- Optimize warehouse design.
- Consider current and future needs.
- Implement an ongoing slotting optimization program.
- Take advantage of vertical space.
- Use multiple storage-shelving configurations.
- Fill more orders faster through automated voice- or action-controlled systems.
- Use an automated storage and retrieval system (ASRS).
- Put brick-and-mortar storage space to use for extra inventory.
- Manage inbound and outbound freight vendors with a robust, precise inbound freight routing guide.
- Use metrics and Big Data analytics for performance measurement and improvement, explains Inbound Logistics.
- Automate, and train staff on how to interact with new systems.
- Consider software-as-a-service (SaaS) solutions that can scale with your warehouse.
- Integrate ALL SYSTEMS, including last-mile delivery and the transportation management system.
Jason Rosing is a founding partner of Veridian; a valued Manhattan Associates partner and technology leader specializing in user-friendly, robust and flexible automated testing and configuration management solutions designed to meet the ever-changing challenges of the omni-channel landscape. This article originally appeared on Cerasis.