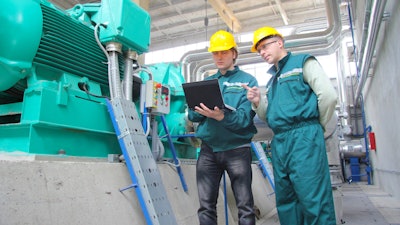
The COVID-19 pandemic has caused extreme disruption to the manufacturing sector, starting with supply issues at its onset. Since then, manufacturers have risen to the challenge, switching production to essential foods, household goods and medical supplies like PPE, demonstrating this sector’s ability to pivot and keep supply chains open and flowing.
Although the manufacturing sector has displayed an innate knack for adaptability, leaders need to ensure this goes beyond systems and production decisions when considering resilience over the long term. In order to create a truly resilient enterprise, these organizations must put equal effort and care into developing their workforce — the second largest expense to most manufacturers, and arguably the sector’s most valuable asset.
As one of the largest employers of essential workers, manufacturers need to ensure they prioritize the needs of their workforce in order to retain and develop talent. Being able to accommodate these needs in an agile manner through technology will ultimately make organizations more resilient to the rapid change that will continue well into the future.
The latest Labor department numbers show that in July manufacturing unemployment rose by 26,000 in the last month, but is down by 740,000 since February. As plants slowly re-open, the economic landscape remains uncertain. As such, new data from Ceridian explores the financial impact of COVID-19 and its effect on the workforce.
The research reveals that 30 percent of U.S. workers said an unexpected expense of less than $500 would make them unable to meet their financial obligations. Forty percent of respondents from the same survey said financial insecurity caused a drop in productivity and engagement in their work life. This sort of financial stress has a direct impact on employee performance. If not mitigated, it can hurt a business’ ability to retain talent.
Reduced productivity is harmful to the business for obvious reasons, but it’s less well known that low engagement is an major indicator for a mass exodus of talent. In fact, 21 percent of survey respondents said they would search for other/additional employment opportunities due to financial instability. Chasing new talent to replace employees that have left is time-consuming and expensive, hindering business productivity overall.
Even with many of its workers deemed essential, the manufacturing industry lost nearly 1.3 million jobs in April following the start of the pandemic, according to the United States Bureau of Labor Statistics. As a result, many are facing financial insecurity, with 80 percent of workers already living paycheck-to-paycheck.
Such employees are poised to greatly benefit from agile solutions like on-demand wage access. With an on-demand pay solution, employees can access their earned wages freely through an app on their mobile device, eliminating the restrictions of a bimonthly or monthly pay cycle. This increased flexibility allows employees to do what is best for their finances, especially in response to unexpected circumstances.
Industry 4.0 and a Shifting Workforce
Although it’s tempting to think this period of economic uncertainty is temporary-- it’s clear the manufacturing industry has been undergoing disruption for some time under the guise of globalization and digital transformation. In this environment, businesses need to be armed with proactive, data-driven strategies to navigate continued disruption.
As previously stated, attracting new talent can be budget- and time-consuming but manufacturers need to ensure their organization will be able to withstand absenteeism. Devising a proactive succession plan that includes critical, non-management roles will minimize risk to production when key employees leave. As an added benefit, succession planning is known to improve retention for high performers looking for opportunities to grow and take on a bigger role.
These plans should also tackle re-skilling and knowledge management. The skills gap won’t shrink with high employment, if anything it will grow even greater, so it’s important to continue developing talent. One key area to focus on is managerial roles. They set the tone for the broader workforce and can greatly influence morale. The plans you put in place now will affect the talent you retain later down the line.
It’s counter-intuitive, but even as most organizations are in a hiring freeze, this is the time to think about investing in talent. Manufacturers should revisit their recruitment, hiring, and onboarding systems, as well as their procedures, to increase efficiency and speed. Technology can help by reducing the administrative burden on HR teams, allowing more time for strategic initiatives, such as training and succession planning.
The pandemic has been one big exercise in agility for the manufacturing sector. It’s easy to think that we’ll eventually settle into a “new normal” – but recall how rapidly the manufacturing sector was already changing before the pandemic. Organizations that integrate agility in this “new normal” and focus on the well-being of their workforce will have a significant competitive edge.
Adam Aguzzi is Senior Principal, Manufacturing Industry Advisory at Ceridian, responsible for working with key customers and prospects in the manufacturing sector. He holds a CPA and an MBA from the University of Toronto.