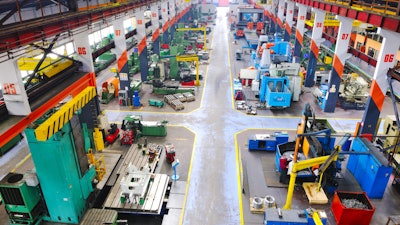
Spring 2020 has introduced unprecedented changes to both business and societal norms. Social or physical distancing is here to stay until herd immunity is established. Manufacturers are re-designing their staffing models and EHS protocols as they work towards protecting staff while managing costs. Lean and Gemba Walks will help ensure value streams are intact while implementing new distancing and safety protocols. In addition, companies are implementing a variety of changes, including:
- Physical distancing of work cells.
- Marked floors for cells and one-way paths.
- New cleaning protocols.
- Mandatory PPE.
- Shift scheduling to minimize population density in the plant.
- Staggered shift starts and static shift partnering to limit hands at a specific station.
It is a difficult balancing act to eliminate potential transmission opportunities while allowing staff liberty and social interactions. However, even with marked unidirectional paths, people movement equals particle dispersion. Maintenance, repair, and operations tasks generally require travelling from point-of-use to the supply room, resulting in both travel time and interactions along the way.
Prior to the coronavirus pandemic, some large manufacturers deployed runners based on tangible benefits. Now that minimizing points of dispersion are important, this model becomes even more attractive.
The Right Model
Operators, machinists and maintenance engineers leave their work area to collect the materials required to complete a work order. This results in travel time to the supply room, inevitable social interactions along the way, and time to locate material or wait for material provision. All of these activities can be potential transmission opportunities.
Another option is the Customer and/or Supplier Managed Supply Room. With this model, users place requisitions at point-of-use via an established workstation or a mobile device - with both utilizing regular sanitizing schedules. Requisitions generate pick-lists at the supply room, allowing for the material to be staged and delivered by a runner.
Advantages of this model could include:
- Limited access to the supply room translates to fewer sanitization cycles, as compared to when many people are in and out of the room.
- Runner is the only individual traversing the plant floor, thus maintaining stable and balanced population density throughout the plant.
- Reduce the number of interaction vectors.
- Placing requisitions when work orders are scheduled have the lean advantage of reducing wait times and having materials delivered near-Just-In-Time.
- Improved productivity and efficiency of maintenance activities are measurable when comparing the hourly cost of a maintenance engineer to a runner.
Take the following scenario as an example:
- 20 employees require material from the supply room on a daily basis at an average shop rate of $50 per hour per employee.
- Assume each employee makes two trips a day to the supply room, 10 minutes per trip including travel-time and wait-time.
- This equates to costs of $6,667 per month.
- The runner makes $25 per hour, or a monthly cost of $ 4,000 per month.
- Eliminating these trips produces a net monthly savings of $2,667 ($6,667 - $4,000).
- The savings does not include recapturing lost productivity gained by keeping the employee at point-of-use.
Introducing technology is typically based on a need for workflow efficiency and improved information access and management. Although it may not be front of mind during uncertain times, it is important to look for opportunities to leverage either existing software or new cloud-based software to support social distancing, which might include:
- Integrating point-of-use procurement with MRO and supply room management, as they can be the low hanging fruit to help reduce shop floor walking traffic and improve operational efficiency.
- Take advantage of flexible, configurable Computerized Maintenance Management Systems (CMMS) to track OSHA regulatory compliance.
- Leverage a fully integrated MRO and secondary spend procurement system that is not encumbered with user fees to enable your key personnel to create requisitions on the go and further minimize shop floor interaction.
If your present supply room is unmanned and you have been considering changing to a manned strategy, now may be the time to do so. Today’s integrated inventory and procurement software solutions have the tools to quickly take you to the next level of safety and efficiency.
Jane Liu works for Tofino Software, Inc. For more information, go to www.tofinosoftware.com