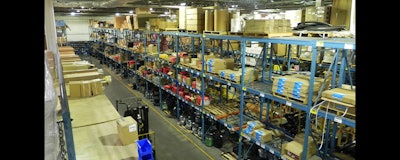
Distributors and warehouse owners and managers around North America are taking steps to reduce their consumption and actively become involved with sustainability in a number of different ways. However, very often they cast away easier and less costly “low-hanging fruit” options and decide to go with more expensive programs that may address just one type of consumption, such as energy, water or fuel.
For instance, a major shipping and logistics company, in an attempt to become more sustainable and cut its annual electricity bill by nearly one-half invested in an elaborate solar panel installation at its approximately 38,000-square-foot warehouse in Lyon, Singapore. The elaborate photovoltaic grid system converts sunlight into alternating current electricity to help power daytime operations at the facility. The entire project cost about $200,000, with an expected six-year payback period.
Of course, this is an excellent step in helping this facility become more sustainable, reduce its energy consumption and eventually reduce its operating costs once the system is paid for. However, and quite possibly, this company could have taken some steps with little or a more modest initial investment to reduce consumption of not only electricity, but other metrics, saving the $200,000 it spent on the solar panels and still producing significant annual savings. Further, these steps would not be limited to depending on sunlight to deliver cost savings. These measures would allow the warehouse to reduce consumption and its related costs during all hours of operation, day and night.
We are accomplishing this among distributors in the professional cleaning industry, and the savings they are enjoying can happen in all types of distributorships throughout the country. The program, which I helped put together with ISSA, the non-profit worldwide cleaning association, is called the Distributor Efficiency Analytics and Learning Program, more commonly referred to as the DEAL program.
It is helping janitorial distributors (jan/san) find that by improving efficiencies* related to consumption and reducing waste, they can cut their operating costs significantly and be more profitable. These measures can be replicated in most any distributorship or warehouse facility.
How The Program Produces Savings
We believe that current jan/san distributors adopting the DEAL program can save a combined estimated $40 million annually, savings that could translate into increased sales by an approximately $400 million annually among the distributors. This is based on the profits and expenses of typical ISSA jan/san distributors.
It all comes down to the math:
- The association has approximately 2,400 distributor members
- These distributor members have about 5,000 warehouses and offices
- The sizes of these facilities range from 10,000 square feet to 100,000 square feet
- The square foot operating costs of these warehouses and offices run approximately $2.50 per square foot, which amounts to $25,000 to $250,000 annually
- According to performance data compiled by the U.S. Environmental Protection Agency (EPA), facilities such as these can reduce operating costs by 10 percent to more than 30 percent when sustainability initiatives are implemented
- This reflects a potential savings for a 10,000-square-foot warehouse of $2,500 to $7,500 annually; for a 100,000-square-foot facility, the savings could be as high as $75,000 annually
Also, it is estimated that these distributors have approximately 25,000 work-related vehicles. Because one of the goals of the program is to reduce the fuel consumption of these vehicles, not only will there be cost savings, but the reduction in greenhouse gases can be significant as well.
The Program At Work
The program we structured, which I repeat can work with most all distributorships, consists of three essential elements: education, benchmarking and an awards program.
Education: Each distributor has access to a data portal, an online dashboard system that can be used on any computer. The portal provides instruction on low- and no-cost improvements — like reducing energy and water consumption — that warehouse operators can make. These are initiatives that lower operating costs. It also recommends that warehouse operators form a team, trained on how to use the portal and the steps necessary to implement the program.
Benchmarking: One of the most important steps is benchmarking. This provides warehouse operators with two types of information: data regarding past consumption and data showing current consumption. Both pieces of information are essential to the success of this program. The data is integrated with information provided by ENERGY STAR and SmartWay. ENERGY STAR helps organizations select products that use energy more efficiently, reducing consumption, and SmartWay is designed to assist organizations that deliver freight in using new procedures and technologies that reduce fuel consumption for their trucks. These programs are designed to reduce consumption by 10 percent to 30 percent, along with related greenhouse gases.
Awards: While there is nothing scientific about honoring people or organizations, appreciation confirms that someone’s work is valuable and typically results in inspiring others to work even harder to be recognized and honored. It distinguishes those distributors that have been able to reduce consumption, become more sustainability-focused, and reduce operating costs.
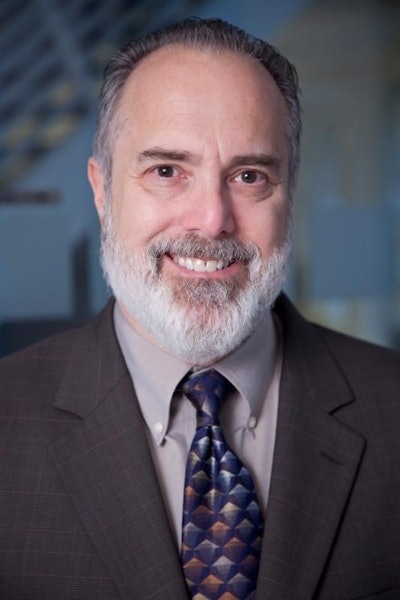
It was not that many years ago that pursuing sustainability within an organization meant spending money to get results, just as the Singapore warehouse we discussed earlier did. However, and quite, fortunately, we are finding sustainability is possible at far less cost and can still result in considerable cost savings for distributors.
Stephen Ashkin is president of Sustainability Dashboard Tools, Inc. and is an industry leader turning sustainability into cost savings. He can be reached through his website at [email protected]
*The term “efficiency” is often misunderstood when it comes to the consumption of natural resources. It is not the same as “conservation.” For instance, water conservation refers to reducing water consumption during a temporary drought, while water efficiency refers to reducing water consumption in the long-term, no matter if water is plentiful or if there is a water shortage.