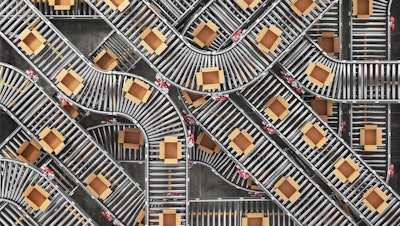
Warehouse management systems have been around for several decades. JCPenney created the first real-time WMS in 1975. Since then, warehouse management systems have become more and more powerful. As a distribution company, you know the importance of an efficient enterprise resource planning (ERP) system, but are you utilizing all the resources available?
A WMS is an invaluable tool that can significantly improve your company’s distribution center and warehouse operations. It helps streamline operations, reduce costs and improve customer service.
Here’s why a distribution company should consider using a warehouse management system:
A WMS allows for better inventory visibility and accuracy. With improved inventory visibility and accurate order fulfillment, you can ensure customers receive the correct items promptly. This can improve customer satisfaction, increase customer retention, and increase revenue. With a WMS, organizations can track inventory in real time and quickly locate items in the warehouse. This increased visibility ensures you always have the right amount of inventory on hand, eliminating costly stockouts and overstocks. Additionally, it can reduce the costs associated with inventory control, as it provides real-time visibility into inventory levels, allowing for more accurate ordering. System-directed cycle counting ensures that every location in your facility is counted in the specified time frame, leading to greater bin-level accuracy.
A WMS also eliminates the need for manual data entry, reducing errors and improving accuracy. Optimizing your warehouse operations can reduce labor costs and improve efficiency. With automated processes, you can reduce the time needed to complete tasks and increase your throughput. This improved efficiency can help organizations meet customer demand promptly through increased throughput capacity and reduce the costs of running your business. An example is directed put-away on the receiving dock. With directed put-away, the system tells the put-away driver what specific bin to put the shipment in based on your criteria. In a manual warehouse, the put-away driver must know what type of bin the shipment can be stored in based on size and weight restrictions. Then they must look for an empty bin of that type to put the shipment in. The location is manually written down to be updated in the system later. These additional steps can increase the time and travel and allow for more errors.
Many products in warehouses may have expiration or use-by dates. A WMS supports a variety of rotation methodologies, such as first in first out (FIFO), last in first out (LIFO), and first expired first out (FEFO) to make sure inventory is rotated correctly. Tracking inventory once shipped by lot codes and code dates is essential to your business when a product recall occurs.
Task interleaving is a critical feature for warehouse productivity. No supervisor or manager likes to see a forklift traveling with empty forks. Task interleaving allows the system to allocate tasks to your workers to maximize their opportunity to be efficient and accomplish the maximum amount of work in the shortest time. The system may direct a picker moving to their next pick location to bring a pallet to the shipping dock along the way. Traditionally, the picker would not know that pallet needed to be moved, nor would the picker get any efficiency credit for doing so. The process allows different functions to accomplish tasks that increase the overall efficiency of the entire operation.
Some features to look for in a WMS include appointment scheduling, inventory management, wave planning and allocation, 3D visual warehouse, receiving and directed put away, task management, picking and packing flexibility, cross-docking, task interleaving, yard visibility, replenishment, kitting and value-added services (VAS), load management, embedded labor management, analytics, voice processing and extensive reporting.
Finally, a WMS can help you stay on top of compliance regulations. With automated processes, you can quickly and accurately identify and track items. This can help you remain compliant with industry regulations and avoid costly penalties.
During a recent conversation with Dan Schuberth, chief revenue officer of the National Association of Wholesale Distributors, he said, “A WMS is the beating heart of any modern physical distribution operation. In addition to the level of control it provides over inventory, fulfillment and transportation, the right WMS harnesses a treasure trove of data to help management teams make the right decisions to optimize efficiency and reduce costs. This is the most critical investment operating teams can make to ensure they can continue to deliver for customers.”
The consequences of not using a WMS can be significant. Without it, a company’s operations will be less efficient, resulting in higher costs, decreased on time in full (OTIF), and reduced customer satisfaction. Manual errors will be more likely, leading to inaccurate inventory levels and incorrect orders.
A WMS is a valuable tool for any distribution company. It can improve efficiency, reduce operating costs and accuracy, and improve customer service. The consequences of not using a WMS can be substantial, so take advantage of its benefits.
Will Quinn is the director of distribution industry and solution strategy at Infor.