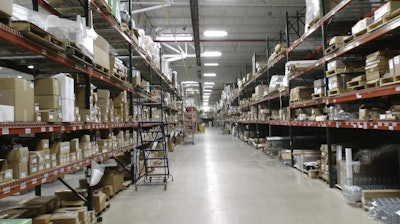
Anyone keeping tabs on the current economic news cycle has undoubtedly seen numerous news pieces about how various employers are struggling to find needed talent amid impacts of the still-ongoing COVID-19 pandemic. Employers are frequently complaining about the struggle to fill open positions, citing ongoing labor shortages due to enhanced government-provided benefits, the public’s concerns about returning to workplaces amid the pandemic, and a sudden rush to find childcare as millions of Americans transition back to physical workplaces after working remotely for the past 18 months or so.
But when most people think of these issues, consumer retail establishments are the businesses that I think immediately come to mind. I’m sure you’ve seen Help Wanted signs posted outside numerous restaurants, bars, retail stores and other local establishments in your area.
But recent commentary shared in quarterly earnings conference calls shows that major industrial distributors are dealing with these same labor issues, along with major headwinds from transportation costs.
In Fastenal’s 2021 second quarter earnings call back on July 13, president and CEO Dan Florness actually opened the call addressing how most industrial suppliers are likely facing difficulty in hiring as the global economy continues to reemerge from 2020 shutdowns that lasted well into 2021. For Fastenal, specifically, Florness elaborated on the issue’s three-pronged impact on the company’s hiring.
Florness discussed how the company hires many part-time employees, and a very large portion of them are full-time students that Fastenal would eventually like to become full-time employees there. With that, Fastenal focuses acutely on four-year state colleges and two-year technical colleges as a talent pipeline. But with COVID closing schools and many students now attending school remotely, Florness noted “a big chunk of our recruiting base has vaporized from the areas that we traditionally approach. And that has created some challenges for us.” He said those challenges have lessened over time, but are still pretty acute.Florness
- For a large portion of the company’s part-time employees, especially in distribution centers, Fastenal represents a second job. Florness noted how despite Fastenal’s scheduling flexibility that it offers, some part-timers have had to pull back on their Fastenal hours due to child care issues or when their second job enacts mandatory overtime.
- Fastenal is seeing some “geographical biases” in hiring demographics in the US, which the company says are dependent on how open or closed the society is and/or what impediments there are to hiring from the standpoint of public policy. The company has also seen a significant disparity on the basis of gender throughout the pandemic. “Our female applications are down about a third from what we've seen in recent years,” Florness said. “And we've seen worse than historical patterns as far as turnover in an environment where society is shut down, and a lot of schools and daycares closed, we've seen a dramatic impact. And that's fallen largely on the female portion of our employee base and our potential employee base, and we're making efforts to improve that, but they're difficult.”
Over at Grainger, chairman and CEO D.G. Macpherson touched on the company’s efforts to acquire and keep talent in the company’s Q2 earnings call on July 30:
Macpherson
Transportation
On the transportation side, both Grainger and Fastenal discussed numerous factors impacting their fiscal bottom line. Macpherson gave the example of a customer in New York, which would typically have their entire order fulfilled from the company’s Northeast distribution center. But due to current supply constraints or production delays, part of the order may currently only be available at Grainger’s DC in Louisville, KY. That order can still be fulfilled between the two, but it adds an extra day and incremental cost to the order.
“Transportation has been very challenging,” Macpherson said. “That is clearly linked to the product and labor shortages. While we have always prioritized optimal routes and cost efficiencies, over the last few months, we have partnered with our carriers in new ways to ensure we are meeting customer expectations. We have also added new partners to our carrier mix to handle our volume and provide us flexibility.
“It's important to note that the overall freight market is volatile and uncertain. While we are confident in our current plans to manage these challenges, there are a lot of moving pieces and constraints across all modes, parcel, LTL and ocean freight. For example, the ocean freight market has been uncertain as the pandemic surges again in Asia and container costs fluctuate.”
Macpherson added that Grainger expects these supply chain challenges to last through the end of the year and likely well into next year.
Florness echoed this sentiment on July 13 and detailed why ocean freight is being especially impacted.
“There's a ton of inflation going on. There's inflation, because of disruption in shipping, i.e. the cost of moving the container, and this is pretty public information, so, I don’t need to cite figures, but it's gotten really expensive to move a container across the ocean. And it takes a longer time than it did 12 and 18 and 24 months ago, because of all the congestion at the ports, and so, massive inflation going on.
“Internationally, there continues to be a shortage of capacity, which has made moving products particularly fasteners increasingly costly and sustained long lead times. We believe this dynamic could persist at its current level of intensity through 2021.”