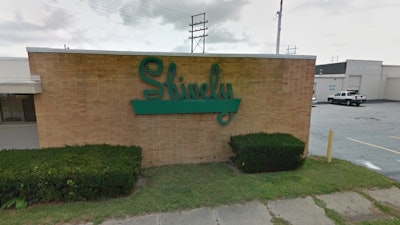
In late 2011, Industrial Distribution travelled to Flint, MI to visit Shively Bros. — a family-run, employee-owned MRO distributor and service provider for ID’s 2012 January/February cover story. Shively first cracked our annual Big 50 List in 2011 at No. 49, and has been a mainstay since, checking in at No. 46 last year. As of mid-June, the company has 410 employees across 13 locations.
ID recently re-connected with Shively Bros. to learn what the company has been up to recently.
Industrial Distribution: How has Shively Bros. grown since our 2012 cover story?
Chris Clarambeau, Shively President: There’s been no new acquisitions lately, but we are seeing more demand from customers for labor support as manufacturers push to reduce their own direct employee counts. This includes professional, skilled, semi-skilled and non-skilled staff. Our most recent physical expansions have been in central Indiana. These locations are more dedicated to service provision to specific customers rather than traditional product sales and distribution.
We are still seeing the trend for manufacturers to outsource tasks not directly related to their product manufacturing. Inventory and supply chain management, inspection services, tool setup and engineering services are still providing growth opportunities for Shively Bros.
ID: For our 2019 Big 50 Feature, Shively Bros. mentioned that it has recently expanded into new industries, made significant e-commerce investments. Can you recap those investments?
Clarambeau: Through its history and to this day, Shively Bros. has served primarily automotive manufacturers. We have a developed a skill set, system and services offering that can be applied in any type of manufacturing and we are targeting more diverse business. Our strategy is to combine our normal approach to selling technical solutions with the efficiency of sales via e-commerce. We do not see that a product sales website will completely replace the face-to face technical problem solving that our staff provides to our customers. We intend to use e-commerce technology to make the purchase transaction easier for the customer and improve the response time in quoting new business.
ID: This past December, the company announced its new management team that was comprised of internal promotions. What’s it been like for the team to have to manage a major industry crisis (the pandemic) just a few months into their new positions?
Like everyone else, we had to change focus and make difficult decisions while maintaining a focus on employee retention. Each day was a new challenge and we had to adapt quickly to new ways of working. One of Shively Brothers’ “Core Values” is problem-solving and that was reflected in how our teams responded to changes.
We were fortunate to obtain the federal “PPP” loan, and we used that to retain our team on payroll once the funds were available. Our customers were not requiring our services nearly as much in April and May, so we used this slow period to make huge progress in developing our new-hire training program and continuing education system we are dubbing “Shively Academy”.
Our 2019 employee engagement survey identified training as a weakness. We used this COVID downtime to turn a weakness into a strength. We are very proud of the result. We were also able to obtain 3500 KN 95 masks that we donated to our local chapter of the American Red Cross.
It was also our goal to implement the “Entrepreneurial Operating System” during 2020. We were able to pull ahead our implementation schedule for this project as well. The downtime provided us with the time necessary to have very in-depth discussions on how to integrate EOS with our already existing ISO9001:2015 quality system. We are now well beyond the point in this project where we originally expected to be by year-end.
While it is an understatement to say that 2020 has come with personal stress levels I have not previously experienced, I can look back with pride on how the Shively Bros. team faced the challenges and lived up to its core values.
At the end of the day, I couldn’t be prouder of not only our management team, but all Shively team members for persevering through these challenges and coming out stronger than ever. I am one to give credit where credit is due and our new president, Chris Clarambeau, provides consistent unwavering leadership and dedication to our organization and to our people. I am beyond grateful for the opportunity to work with him and I value his mentorship dearly.
Terry Bernalis, executive vice president: Well, to say there were a few anxious moments would be minimizing the reality. Although Covid-19 was and continues to be a major health crisis our initial concern was the financial well-being of our team members, and long-term sustainability of the company. Our focus was centered around keeping team members on payroll, maintaining their critically needed health benefits and retaining talent.
ID: What actions did Shively Bros. take to protect its employees and continue to serve customers during this the COVID-19 pandemic?
Shively-Wolgast: We set up and distributed new laptops for individuals who were using desktops prior to the pandemic and began having all laptop users work from home. Our customer service and engineering teams were able to stay engaged with their customers remotely. We developed very stringent safety measures recommended by the CDC and secured the necessary PPE to implement them. We began to slowly bring warehouse, shipping and delivery members back on site to manage any incoming/outgoing shipments taking place. We kept in constant contact with the purchasing group from our largest customer to make sure we released orders in a cadenced timely fashion and requested that our vendors continue to hold shipments while we worked through this.
Though we are not out of the trenches of this pandemic, nor is it likely that we will be for quite some time, we find ourselves in a good place and will continue to strive for the best possible outcome for all of us.
Bernalis: Although we had reduced staff in our facilities, we continued to meet customer demands. Many protocols have been put in place ranging from working remotely when possible, to increased cleanings, temperature screenings, masks and more.