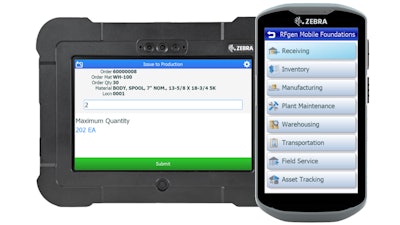
The time for digital automation is now. Industry-wide, distributors are feeling the impact and pressure of supply chain shortages and rising customer demand. Further, as the search for top talent rages on in the Great Resignation, many industrial distributors are turning toward technology to optimize their operations.
One study found that the majority of warehouse executives are making an active plan to invest in new technology to stay competitive, with 40% citing faster, more transparent delivery as a top driver for growth going forward.
But before distributors can delve into large-scale technology projects, they must put an emphasis on the basics. Automated data transfer options like mobile barcoding can help streamline points throughout the supply chain and across the warehouse, all while connecting to mission critical business systems.
By cementing this type of real-time data flow into your inventory operations, industrial distributors will be better poised to embrace the digital environment and lead with intention and visibility. Here are three ways to get started with automation technology and mobile barcoding.
Review your current processes
Modernization starts with an understanding of the basics. How does data flow through your distribution center? What is the process to get a product from the field onto the floor and into shipping? How quickly does this information feed into your ERP system?
Too often, distributors are not aware of the impact – and drain – their processes have on overall operations. Manual or outdated processes can result in substantial loss, both in time and investment. One study found that smaller operations lose approximately $386,170 a year due to manual operations. An enterprise level organization’s cost is upward of $3.69 million per year.
While manual processes waste time, labor and money, a do-it-yourself digital process can be just as costly and error prone. If digital automation is not fully embraced across your organization, the result is ineffective processes that negatively impact future growth.
Optimizing your existing processes, whether they be manual or outdated, is critical. Mobile inventory solutions like mobile barcoding have direct ties to improved accuracy, efficient workflows and increased reliability.
Take, for instance, automotive parts supplier Brabant Alucast. The company was using a hybrid data collection process, including a legacy ERP system that was only partially automated. The system was ripe for errors, not to mention slow and costly.
By updating their ERP and coupling it with a carefully selected mobile barcoding solution, the company was able to increase operational flexibility and reduce overhead costs. After only six months, stock reliability increased from 70% to 96%.
Pay attention to your inventory
Inventory management is essential to the distribution cycle. Awareness and visibility into your inventory, and its status, can be a make-or-break moment for any warehouse. That’s why accurate inventory is so important.
Mobile inventory software allows organizations to automate data collection. By coupling the technology with barcode scanners, industrial distributors can track inventory throughout the supply chain from the field to the warehouse floor.
Automated inventory management and mobile barcoding improve inventory visibility, enhance shipping efficiency, and increase data accuracy. Plus, this type of software integration directly impacts traceability, especially in the event of a recall.
A recent survey found that 81% of food companies were using either paper-based on partially automated systems. When a recall occurred, only half of them could take immediate action within hours – a now standard expectation.
Mobile barcoding and automated inventory management software are essential to agile business practices. From recall readiness to quickly changing customer demands, reliable data capture is needed to embrace and conquer change.
Address labor shortages
Many companies, across numerous industries, are suffering from another issue: lack of skilled labor. Demand continues to increase, but insufficient bodies on the warehouse floor prevent many from rising to meet it.
That’s why an organization must automate processes to remain competitive. Every minute employees spend on unnecessary supply chain processes is a moment taken away from your core business functions.
Collecting data on the factory floor and entering it later into business systems is error-prone and thankless work for your employees, as well as a waste of valuable staff time. Mobile barcoding technology helps streamline data and gets it from your people and into your systems faster. Plus, easy-to-use interfaces equate to less training time for new hires and more time ensuring your product is delivered on time.
In addition, if your distribution center is large, mobile barcode scanners increase mobility for workers. No longer is someone tethered to one location. Rather, data is captured efficiently, allowing employees to enter inventory data in milliseconds.
But what if your company operates across a wide territory where cellular or wireless coverage is tricky? Many mobile barcoding technology options offer field mobility solutions such as tablets, smartphones or mobile computers that maintain access to critical systems. Data is collected off-line and automatically uploaded once a connection is re-established.
The time is now to embrace digital automation
Digital transformation is impacting every industry. By deploying mobile barcoding, mobile applications and updated critical business systems, distributors can begin to chart a more successful path forward. These options allow for flexibility, work within existing infrastructure, and have a proven history of strong ROI. Mobile solutions should be top-of-mind as you embrace a digital-first mindset.
Rob Brice is the president and chief technology officer of RFgen.