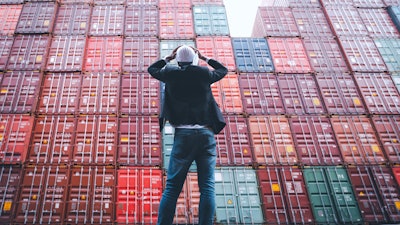
The COVID-19 pandemic has altered the way companies operate indefinitely. The health crisis has impacted everything from employee interactions, health and safety protocols, consumer behavior, routes to market and ultimately, the supply chain.
Supply chain unraveling commenced with pandemic-related lockdowns in Asia, causing the shutdown of factories, leading to shortages of product made overseas. Los Angeles and Long Beach port congestion and lingering product in jam-packed warehouses caused by lack of labor, truck drivers and warehouse workers led to involvement from the Biden administration.
Many industries and companies experienced pandemic-related supply chain ramifications — shortages in toilet paper, flour, exercise equipment, electronics, lumber and more. The automotive sector has been hit hard by the pandemic, struggling to meet demand and maintain manufacturing processes with the shortage of semiconductor chips.
Business sustainability and continuity have appropriately become the primary focus of many companies. A robust Business Continuity Plan (BCP) plays a critical role in constructing a secure future for an organization to navigate a crisis. A BCP is a reactionary protocol for unexpected or catastrophic events that companies can utilize in situations such as natural disasters, pandemics, cyber-attacks and more.
Many informed and strategic suppliers, whether domestic or international, will only do business with companies that have established BCPs and require proof of the fact. Some require verification that BCPs have been tested and are current before contracts are signed to ensure that the supplier can recover from disruptions quickly and effectively to reduce the potential impact.
What Makes Up a BCP?
Two significant themes in an effective BCP are risk and visibility — essential personnel need to understand the level of risk that can impact the business and know which suppliers are critical to sustaining business operations. Digitization of supplier information makes testing and implementing BCPs possible. Unfortunately, this isn’t the standard for all companies as studies show that 69% of companies do not have complete visibility of their supply chain.
Business continuity plans help businesses operate both short-term, such as returning to work or mitigating real-time vulnerabilities, and long-term, such as diversifying the supply chain and creating stronger supply chain resilience. Here are points that a BCP should address:
1) Risk Assessment – Evaluate and prioritize the company’s risks and exposures and establish how to mitigate those risks.
2) Business Impact Assessment – Identify Recovery Point Objectives (RPO) and Recovery Time Objectives (RTO). Establish critical business processes and workflows and necessary staff including primary, secondary and backup contacts.
3) Communication – Prepare alternative communication methods in case standard methods fail. Draft emergency statements and make a list of who to contact in the case of an emergency.
4) Paramount parts of the business – Focus efforts on maintaining the most crucial business aspects that ensure employee safety and restore operations to normal levels.
5) People – Ensure that the workforce and those who are impacted due to a halt in business operations are safe. Designate stakeholders who need to make decisions and undertake critical roles within the plan. Provide education and training for those responsible. Make sure staffing lists are up to date.
6) Redundancy – Diversify by sourcing backup suppliers and determining different locations from which to operate parts of the business, temporary storage sites, etc.
7) Equipment – Source alternative equipment or shift existing equipment to maintain company services. Consider utilizing short-term resources or outsourcing work to other suppliers.
8) IT infrastructure – Establish backup systems for company files and records that employees can access remotely. Ensure adequate cyber security protections. Make sure to differentiate between IT disaster recovery and business continuity.
9) Legal – Plan for possible legal and regulatory issues. Assess whether regulatory agencies need to be informed about events such as a business shutdown or the release and storage of materials.
10) Time limits – Consider time limits such as temporary storage sites and leases. Can the business function on limited or restricted service provision?
11) Integrate Plans – Integrate evacuation, lockdowns and emergency response plans into the BCP.
Mock Scenario Drills
Once a BCP is created and addresses the eleven points above, it’s time to test it through mock scenario drills. Appropriately testing a plan's effectiveness will reveal weaknesses that need remediation and allow procurement and supply chain leaders to better prepare for future interruption events. The plan should be subjected to various simulations via desktop and in real-time. It’s critical that individuals responsible for enacting the plan are aware of changes made and familiar with the latest iteration.
BCP Template
Business continuity is expansive. Each stage from implementation, to business impact analysis, to training, can be involved and intimidating. Avetta, a supply chain risk management software provider, offers a template and use case for businesses to reference in their BCP journey.
The pandemic’s impacts shined a light on inefficiencies in companies’ operations and supply chains, but it also highlighted companies that had a BCP in place to react quickly and move forward efficiently. Make sure your company has a playbook to support potential global disruptions while establishing long-term supply chain resiliency.
Danny Shields