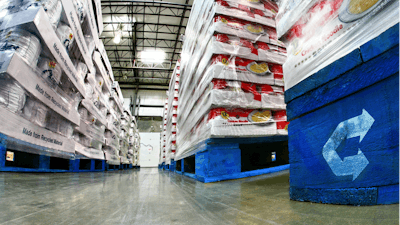
A blanket of clouds swallows the truck yard in thick fog – almost as if the sky knows an intruder is walking the night. In an instant, several semi-trucks are stolen from a large distribution center.
By the following day, it’s safe to assume the business owner will notice and call the police. After all, just one semi-truck can weigh up to 25,000 pounds and cost tens of thousands of dollars. This type of significant loss tends to draw immediate attention. But in supply chain theft, this isn’t always the outcome.
Take pallets, for example. While the value of these shipping platforms is undeniable, a missing pallet here or there can fly under the radar at first. It’s not like waking up to see an empty truck yard. Yet, the cumulative impact of these missing assets is substantial and burdens partners across the supply network, from manufacturers and distributors to retailers and, eventually, end consumers.
Let’s explore the impact of pallet theft a bit deeper – and the steps an organization can take to reduce it.
Recognize the Value of a Pallet
As many industry professionals experienced firsthand, pallet demand significantly outpaced supply during the pandemic, causing availability issues compounded by increasing market volatility. These constraints impacted the end-to-end supply network by disrupting production, exacerbating inefficiencies and hiking prices. Unfortunately, these conditions also attracted some opportunistic bad actors. Entire crime rings emerged to target wood and plastic platforms and resell them as whole units or raw materials. This worsened an existing scarcity problem.
For the first time, it became clear to many folks that shipping platforms are crucial to the global economy. After all, 93% of goods worldwide are transported in the form of a palletized load, according to Virginia Tech’s Center for Packaging and Load Design – so when availability dips, the impact on businesses and ultimately consumers is even more significant.
Disregarding the value of pallets comes at a cost, and not just financially. In addition to decreasing revenue, theft can negatively impact brand reputation by associating nefarious activity with your company and employee attrition by potentially making employees feel unsafe and unproductive. The good news is that there are simple ways to combat these risks by educating employees, keeping partners involved and taking a fresh look at operations.
Foster an Ownership Mindset
Every pallet touchpoint is an opportunity to protect an essential supply network asset, regardless of whose property it is. Instilling an ownership mindset among employees is a great way for leaders to ensure accountability. Often this requires training and education across all levels of the business.
Does every employee understand the value of these assets and handle them with equal care? Does every employee know the types of pallets and where they should be sent? For instance, some stay within the business in a closed-loop system, while others are rented as part of a circular business model. Knowing where a pallet should go next – whether to a manufacturing production partner, distribution center, retail store, recycler or sorting and repair center – makes all the difference in keeping the supply chain moving efficiently. Overall, it’s essential that pallets being loaded or unloaded from a distributor’s truck are in the right place at the right time.
Investing in this type of employee education is good for business. It increases revenue by avoiding operational downtime caused by lost or stolen platforms and creates a safe, optimized working environment for employees.
Evaluate Risk with Partners
While internal training and education are excellent first steps to prevent asset loss, it’s equally important to consider external parties. One crack in a partner’s security ecosystem can cause a ripple effect across the supply chain.
Promoting a feedback loop with partners keeps communication lines open to discuss potential weak points and solutions. In these conversations, transparency is key. What security is in place along a pallet’s journey and how does it fluctuate? Is there visibility into unintended channels or flows that might steer assets to the wrong destination?
Questions like this have led many organizations to adopt new technologies that support real-time tracking and data collection. A Gartner survey revealed that 82% of CEOs in supply chain-intensive industries plan to increase investments in digital capabilities across their enterprise. Over time, these advancements, like pallet tracking technology, will help identify vulnerabilities with high accuracy, facilitating data-driven conversations with supply network partners and customers.
Review Operational Security
With proper education and dialogue in place, it all comes down to execution. Many of the techniques already used for general operational security can also be applied to platform use and misuse.
For example, companies should safeguard operations during off hours by reviewing security measures for a closed or understaffed facility. If needed, it might make sense to increase security in these scenarios by hiring more personnel or installing a new security system. Facility managers should also carefully control who can access sensitive information regarding logistics, delivery routes and storage addresses. If an illicit activity is detected – buying, selling, trading, discarding or otherwise using pallets in unauthorized ways – they can report it to the pallet supplier. From there, the supplier can take action to recover the platforms for proper use.
It’s in everyone’s best interest to protect pallets to keep the supply network moving. The humble pallet isn’t so humble anymore – it deserves the same attention as a finished good because, after all, it’s the critical piece required to move goods to the people who need them and, ultimately, gets product into the hands of the end-consumer.
Jim Congrove is the director of asset control at CHEP.