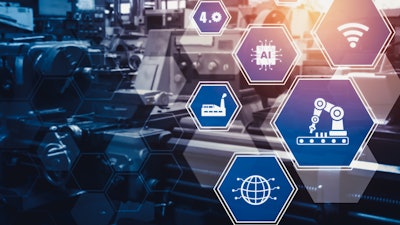
Small and medium-sized manufacturing enterprises (SMEs) face many obstacles and difficulties (economic, technical, cultural, etc.) when it comes to implementing Industry 4.0.
"These are transition processes that are economically costly, and in which SMEs often come up against technical and cultural problems, as they are not cognizant of how to make this transition, or of the benefits their companies stand to gain by implementing Industry 4.0," explained UPV/EHU pre-doctoral researcher Víctor Ramírez-Durán.
While several pieces of work address the incorporating of Industry 4.0 technologies into the sphere of product lifecycle and supply chain, which SMEs could use as a reference, this is not the case as far as the customer life cycle in concerned. In this respect, in a piece of work conducted by the UPV/EHU's BDI research group, a methodology has been developed to assist professionals in SME software departments in the task of creating new software services aligned with Industry 4.0; using low-cost options, this would enable them to change the way customers interact with companies and the experiences they have while interacting with them.
"Industry 4.0 technologies can help to better understand customers, improve their experience when interacting with products, and facilitate enhanced after-sales support," said Ramirez, author of the work.
Semantic technologies and 3D visualization
The proposed methodology describes a series of well-specified phases and activities that are easy to understand and implement, and which can make this transition possible by using minimal financial resources and taking advantage of new technologies.
"With this methodology, it is possible to identify the shortcomings that a company may have with regard to customers, and to analyze how services can be generated in a way that would improve how the customer is treated. The methodology is general; i.e. it does not say which services need to be implemented but helps to spot the shortcomings that can be remedied by generating new services," said Ramírez.
The methodology is mainly based on the use of semantic technologies and 3D visualization. Semantic technologies, in this case ontologies -a network or system that specifies the existing relationships between the concepts of a domain or area of knowledge- provide a high degree of flexibility for the description of knowledge, and also facilitate inference and reasoning processes that are difficult to achieve using traditional databases. On the other hand, 3D visualization technologies offer improved visual representation including better graphics and navigation controls, allowing the user to enjoy an enhanced, interactive experience.
As the researcher explained, this methodology could be used, for example, to create an improved catalogue of a company's products through the 3D visualization of models and advanced navigation options, "with precise descriptions and characteristics of different parts of the model. It could also be used to create a search module which suggests to the customer which product he or she needs".
Another of the examples highlighted by Ramírez could be a virtual technician to improve customer service once the product has been purchased. However, Ramírez pointed out that "the methodology is designed in a practical way so that each company can carry out an analysis allowing it to solve a range of problems in relation to its customers. All these benefits will improve the relationship between the customer and the company and achieve a high degree of customer loyalty."