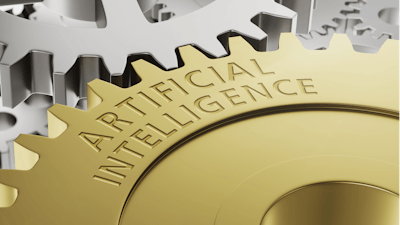
In March 2020, few would have thought of industrial manufacturers as early adopters of new technology. Traditionally a conservative industry, each new technology is carefully evaluated before potentially disrupting very complex and consolidated processes. But the industry is facing unparalleled challenges, propelling cautious companies to quickly adopt disruptive tech to deal with a new reality: a world of irregular customer demand and an increased need for agility in the production line.
Today’s manufacturers need to deliver the same number of products with fewer people, without sacrificing quality due to decreased human oversight. For many, increased utilization of technologies like AI and leveraging the vast amount of data produced in the manufacturing process have become priorities.
Once a nice-to-have technology, AI is now a must for advanced manufacturing – even though the majority of global CEOs expect it will take 3-5 years to fully realize the technology’s ROI.
The ROI issue is therefore critical: while AI may be the answer, it is even more important to have a well-formulated question. Today, more than ever, having a clear business goal in mind for effective AI integration is key. AI does not come one-size-fits-all, and the boundary between success and failure in AI deployment comes down to having a specific purpose that can be tracked and measured with explicit KPIs.
For instance, one simple way to measure business value of AI deployment is analyzing defective products. Producing defective items has never been an option for manufacturers, but in a post-pandemic world this issue is compounded by a more sparsely populated production floor. Adopting AI by multiplying the “number of eyes” looking at the line can eliminate product recalls, increase production yield, boost customer satisfaction, and improve manufacturers’ overall bottom line.
Take a commercial bakery as an example.
Bakeries commonly handle large volumes of ingredients where occasionally a supplier provides the wrong items – sometimes, wrong product coming in with the right barcode. Here, AI can be implemented effectively by adding inexpensive cameras in key steps of the production flow, recognizing ingredients visually and comparing that information to the scanned barcode, correcting errors before the ingredients are stored and used, improving the overall production of the bakery while minimizing waste.
In the example above, a clear objective (reduce waste by a certain dollar amount) is critical. And, the manufacturer can implement an AI solution with specific software/hardware requirements and installation timeline to meet those objectives in a cost-effective fashion.
Today, there are AI solutions in the market that make it easier for manufacturers to retrofit existing hardware and easily add AI as a “software update” on top of established infrastructures.
This reduces that ROI horizon I mentioned earlier from the 3-5 years to mere months.
As these technologies become more robust and streamlined, the business case for AI is getting more robust as well. This is echoed by the rise of AI-powered software, already used for everything from assessing component presence in packaging machines to custom label checking to pallet inspections.
Industry 4.0 adoption in manufacturing necessitates a clear business rationale and measurable KPIs. Despite its widely negative impacts, the 2020 pandemic has catalyzed manufacturers to think more deeply and urgently on these issues—and the conclusion is clear. AI is indeed a paradigm-shifting technology that realizes enterprise ROI by augmenting the human workforce.
The future factory will exhibit a more balanced division of labor between humans, AI, and machines, working synergistically to power the next wave of manufacturing competitiveness.
Max Versace is the CEO and co-founder of Neurala.