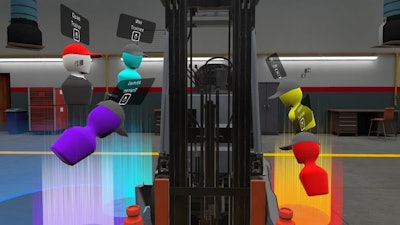
Toyota Material Handling (TMH) has partnered with a Toronto-based virtual reality (VR) company – VR Vision – to provide VR learning resources that will supplement existing training programs for onboarding service technicians and other professionals.
“Our vision is to provide a learning environment that resonates with current and future generations of technicians,” said Holly Brotzman, TMH’s Dealer Training Manager. “While hands-on product training is our preferred method, we realize that not all of our dealerships have the luxury of product inventory, especially heavy-duty equipment. VR technology allows us to supplement existing training programs in an environment that’s accessible to our entire North American dealer network.”
Toyota Material Handling is using Meta Quest (formerly Facebook/Oculus) to create virtual reality training programs and has leaned on VR Vision for the creation of content in a 3D platform as well as LMS integration, device setup, and change management consulting, among other things.
TMH and VR Vision believe this training alternative will become a low-cost and scalable option for businesses routinely training new workers on existing and future products.
In this collaborative multiplayer VR training simulation, which integrates digital twinning and modeling of material handling equipment, users are immersed in a 3D environment where they can connect and interact with the truck, parts, and tools from anywhere in the world. This real-time interaction between users and trainers drives a new kind of learning to help prepare professionals for an industrial environment.
TMH has purchased 300 units to be deployed across North America with future plans to expand from parts identification to more complicated maintenance and repair procedures focused on complex systems.
“While the tech industry is busy debating what the metaverse will become, the team at Toyota Material Handling is staying ahead of the times by deploying secure and scalable virtual reality solutions,” said Roni Cerga, VR Vision CEO. “These programs connect clients and employees from anywhere in the world and give them the ability to collaborate on complex real-time procedures. This partnership only reinforces Toyota’s position as a clear leader in innovation and within the material handling industry.”
Clients including TMH have talked about how the VR Vision system allows for training to be streamlined while also providing value in learning automation. The immersive learning courses provided through these simulated systems are designed to deliver value to companies needing to meet high standards in terms of safety and operational training in the modern world.
“Consistent, convenient, and easily replicable training programs are important to Toyota,” said TMH Instruction Designer Darin Cottle. “Our team uses Toyota Certified Trainers at our dealerships to teach most of the courses offered to our technicians. We are always looking for ways to enhance our training offerings, and the VR Vision system does just that.”