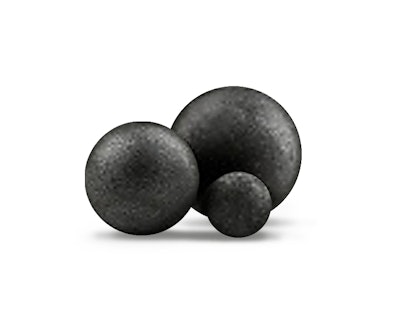
Washington, PA - Ensinger Engineering Plastics offer frac balls for successful fracking operations. During the fracking process, it is necessary to isolate sections of the well. This is accomplished by using specialized equipment known as packers and frac sleeves. Once this equipment has been sent to the proper depth, fracturing begins by sending precisely sized frac balls down the well. Each ball is designed to fit securely into a seal of the same size in the frac sleeve. The frac balls, starting with the smallest and ending with the largest, travel as far as they can until they seat securely in the seal designed to receive it. Positive pressure on the ball and the seal forces the sleeve to open exposing ports through which controlled explosives are directed, creating the desired fracture in the rock formation. This process is repeated as many times as necessary to fracture the entire target zone. The frac balls then either flow out or can be easily drilled out, and oil or gas production can begin. Frac balls have been made from several different materials depending on the number of factors such as temperature, chemical, and impact resistance. The material must also be able to hold up under pressures as high as 10,000 psi. Engineering plastics such as TECAPEEK® and TECATOR have been successful as well as material such as G10. TECAPEEK ST is a new higher temperature PEEK that offers better strength and stiffness, and gives engineers even more flexibility to design for harsher environments.
For more information, please visit www.ensinger-inc.com.