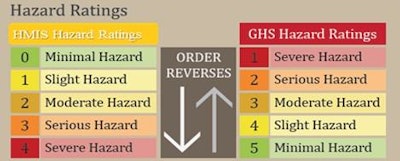
OSHA announced that in 2013 Hazcom (Hazard Communication) 1910.1200 violations were the second most frequently cited standard of the top 10 violations in workplace compliance inspections. OSHA publishes their Top 10 list annually to inform employers about commonly cited standards, so they can take steps to comply, identify hazards, protect employees and ultimately avoid citations.
Besides training employees on the new GHS (Global Harmonization System) labeling elements, new pictograms, and the new SDS (Safety Data Sheet) format, there are more important challenges to compliance, that many employers and Safety Managers may not even realize.
The best way to explain how employers can effectively comply with the new GHS rules is to first break things down into two categories:
- Employer Responsibilities
- Manufacturer/Distributor Responsibilities
The figure below published by OSHA describes the responsibilities of both parties and the dates each must comply with certain changes and/or implementation of GHS programs.
This article focuses on employer responsibilities, so let’s start with the December 1, 2013 requirement for employee training. Employers were required to train all of their employees on the new GHS labeling elements, pictograms and newly designed SDS format by December 1, 2013.
GHS Labeling:
The new manufacturer GHS label for chemical containers must have six elements. Employers are required to train Employees on these new elements and the new GHS pictograms:
- Product Identifier (Name of the Chemical)
- Signal words (Danger or Warning or None, depending on the Hazards of the Chemical)
- Pictograms (Nine different pictures that Display Specific Hazards)
- Hazard Statements (Physical, Health or Environment Hazards)
- Precautionary Statements (General, Prevention, Response, Storage & Disposal)
- Company Information (Manufacturer and/ or Distributor Information)
The Six GHS Label Elements:
New SDS Format:
The new SDS has 16 sections, listed below. Employers must train employees on the new SDS format. What should also be important to employers and Safety Managers is the name change. OSHA officially changed the name of the MSDS to SDS. It turns out that this name change gives them an edge during an inspection. As a former OSHA Compliance Officer, I can tell you that one of the things we always looked for was a prominently displayed MSDS book in the workplace.
Today, if a Compliance Officer sees your old MSDS book proudly displayed in the workplace, they know to ask questions about your Hazcom/GHS training programs. Chances are that you are likely a good candidate for Hazcom/GHS citations. However if they see an “SDS” book displayed in your workplace, they immediately know that you are likely up to speed on the new GHS regulations. So a single name change and changing your cover on your old MSDS book to SDS could help in avoiding Hazcom citations.
The 16 sections of the New SDS:
1. Identification of the substance or mixture and of the supplier
2. Hazards identification
3. Composition/information on ingredients
4. First-aid measures
5. Fire-fighting measures
6. Accidental release measures
7. Handling and storage
8. Exposure controls/personal protection
9. Physical and chemical properties
10. Stability and reactivity
11. Toxicological information
12. Ecological information (non-mandatory)
13. Disposal considerations (non-mandatory)
14. Transport information (non-mandatory)
15. Regulatory information (non-mandatory)
16. Other information, including date of preparation or last revision
Workplace Labeling: The Biggest Problem
So, as you can see training Employees to meet the Dec. 1, 2013 requirement is relatively easy for employers and Safety Managers because you only have to teach your employees about the new GHS label and the new SDS. That said, the June 1, 2016 requirement for employers to have a workplace labeling system for secondary containers is a much more challenging task.
Here’s why it’s difficult. We are all familiar with the old HMIS (Hazardous Material Identification System) to label workplace containers. We use it whenever we migrate a chemical from its parent container to a secondary workplace container as shown below.
The problem is that the HMIS number coding system is NOT concurrent with the new GHS Hazard Classification number codes. The two are in fact reversed. If you already have a hard time getting Employees to label secondary containers, you now have an even bigger problem. Employees will have a difficult time finding HMIS numbers on an SDS and they may confuse these numbers with the GHS Hazard Classification numbers. See the figure below that shows the reversed order of the two systems.
OSHA has stated that Employers can use any system they wish for workplace labeling as long as it conveys the hazards of the chemical. Employers must understand that GHS is a Globally Harmonized System for classifying chemicals internationally for trade. The unfortunate truth is that other countries do not use our HMIS system and HMIS ratings for chemicals are not a requirement in any of the 16 sections of the SDS. Employers need to actually consider discarding the old HMIS rating codes and come with a workplace labeling system that is concurrent with GHS label elements.
OSHA says that you have until June 1st 2016 to develop a workplace labeling system.
A more appropriate workplace label would convey the elements of the GHS labeled parent container. Holding on to an antiquated HMIS system is a recipe for potential disaster and certain to be a great way to get someone hurt or receive an OSHA Hazcom citation. Employees will rather not label a secondary container than try to figure out the appropriate hazard class numbers.
A workplace label is a much more efficient and safer way to label secondary workplace containers. Employees need only look at the elements of the GHS labeled parent container and they have enough information to properly label the workplace container.
In Summary:
OSHA is determined to cite employers that do not comply with the new Hazcom Standards and GHS. This is evident by Hazcom Violations being the second most commonly written citation by OSHA nationally.
Training employees on the new six elements of a GHS label, pictograms and the new 16 section SDS format is easy and should have already been completed in December 2013. If you haven’t trained your employees you are already in violation of the new Hazcom standards.
The greater challenge for employers is having a workplace labeling system in place by June 1st of 2016. The old HMIS system is just that, old and out dated. Globally, HMIS is not a requirement on an SDS and serves only to confuse employees, causing them to take the easy ways out. Your workplace labeling system must be easy to use and must convey need to know hazard information that is globally acknowledged to keep employees safe.
For more information on GHS and workplace labeling go to: www.stop-painting.com