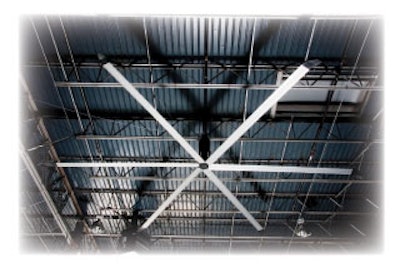
This article first appeared in IMPO's July 2012 issue.
The loading dock: an essential yet often overlooked link in the supply chain. Valuable product enters and leaves a facility through this dynamic, integral, and potentially hazardous warehouse portal. Trailers need to be secure, workers need to be comfortable, and facility managers need to be able to effectively manage loading dock activity even as they look to cut costs and increase efficiency.
Worldwide economic turmoil and increasing energy costs are forcing facility managers to maximize profitability, and the loading dock presents an ideal area to cut costs. Energy solutions like LED dock lights and door perimeter seals, as well as new yard and dock management software can help workers at the loading dock do more with less, preventing a material handling standstill.
Comfortable Efficiency
“The basic needs of the material handling industry have not changed in recent years,” says John Carroll, director of U.S. sales at 4Front Engineered Solutions, manufacturer of truck and loading dock equipment. “We are still seeing a major focus on safety, efficiency, and low maintenance costs as the top needs that customers are seeking to have their dock equipment meet.”
While basic loading dock needs remain unchanged, the ways in which those needs are being met are changing. State of the art technology is creating new and improved methods of energy savings and sustainability, creating a safer—and more comfortable—loading dock for workers. Advances in dock door and seal materials and engineering now allow companies to realize increased energy efficiency and savings year round. “A universal change that has affected the material handling industry over the last few years is the interest and sense of urgency to find energy efficient warehouse solutions,” Carroll says. TKO Dock Doors are designed for efficiency and are able to withstand “moderate to severe” panel and track damage, and high winds. Carroll adds, “with a patented track, panel, plunger, and weatherseal system, TKO doors help facilities realize substantial energy savings and reduced maintenance costs.” Tight perimeter weatherseal helps eliminate air and light infiltration and the seals are attached to the door panel instead of the door jam, keeping them out of harm’s way to provide a consistent seal. An effective air barrier can also contribute to employee comfort.
“Comfort of employees at the dock is paramount,” says Carroll, “and now more than ever, companies are learning that comfortable employees are more productive employees.” He explains that ventilation and air circulation at the loading dock are two areas that can increase employee comfort through the use of truck cooling fans like the HV-ES™ and HVLS fans for cooling entire warehouse spaces. “The HV-ES Air Exchange Fan creates a focused column of air that forces hot, cold, or musty air from the trailer replacing it with fresh air.” HVLS fans, designed to create a comfortable environment while maintaining an efficient facility, produce large, cylindrical columns of air inside the facility.
Focus On Safety
“A big safety issue warehouse and distribution facilities face is keeping a trailer securely restrained at the dock door while loading or unloading is occurring,” says Carroll. To prevent vehicle creep/dock walk (premature vehicle departure) accidents, vehicle restraints can be used to keep the trailer tightly encased at the dock. Available in both mechanical and powered models, an electronic vehicle restraint system incorporates other loading dock equipment such as dock levelers, dock seals, overhead doors, and signal lights to ensure clear communication to loading dock workers and drivers.
“Safety on the loading dock involves clear communication between dock workers and trailer drivers,” Carroll adds. Utilizing communication lights reduces the potential for serious accidents from drivers pulling away before the loading or unloading process is complete. LED dock lights are bright and effective and can save a significant amount of energy compared to traditional incandescent bulbs.
Running your loading dock with inefficiencies can lead to a whole host of problems—shipment delays, product damage, accidents, and injuries. “Customers are striving to do more with as little as possible,” Carroll says, “which puts more pressure on the dock workers, truck drivers, and equipment to perform at their peak levels at all times.” New software can interface with loading dock equipment to help facility managers monitor activity in the yard. Carroll explains, “4SIGHT Dock and Yard Management System uses state-of-the-art technology to provide facilities with increased visibility, productivity, and sustainability in their yard, loading dock, and warehouse.”
“From the moment a trailer enters your yard to the time it leaves, you’ll know exactly where it is, what’s on it, where it needs to be, and how to get it there as efficiently as possible.” Utilizing RFID and GPS data, 4SIGHT provides real-time information to help facilities keep track of all activities within their yard, and is able to monitor a variety of critical performance analytics, including temperature-sensitive loads; overflow yard areas; and trailer status, storage dwell time, and inventory.
“From scheduling to reporting,” Carroll explains, “4SIGHT Yard helps you increase productivity from the time a trailer enters the yard until the time it leaves.” The system produces an image of current loading dock status, allowing users to see the entire loading dock operation on one screen. Tracking inbound and outbound product locations, users can improve yard and dock management by minimizing data errors and time consuming calls with dispatch personnel and truck drivers by reserving loading dock doors for completed trailers. The priority doors can also be activated offsite—loading dock doors can be opened with an iPhone/iTouch interface.
“4SIGHT Yard and Dock Management System can help eliminate bottlenecks at the dock and in the yard to greatly improve efficiency and assist facilities in safely doing more with less,” says Carroll. Able to be integrated into existing loading dock equipment, 4SIGHT tracks loading dock usage and can notify a maintenance manager when loading dock equipment is due for maintenance. “4SIGHT’s Dock Management System keeps the dock running at optimal efficiency by collecting critical equipment analytics that no other systems can provide,” he explains.
“Now, see the entire loading dock, discover areas to increase efficiency, and keep your facility running at peak performance.”